B.H.E.F & STAR EDUCATION Summer S.T.E.A.M Academy
KIDSTARTER

Words of Wisdom
"Engineers like to solve problems. If there are no problems handily available, they will create their own problems."
Scott Adams
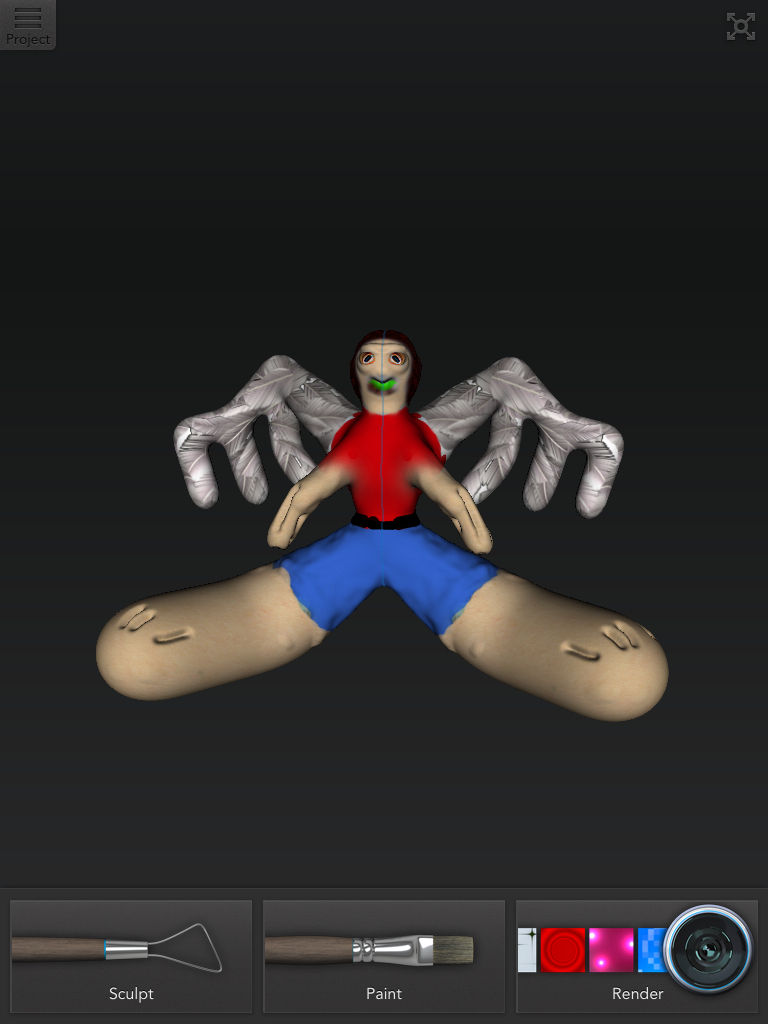

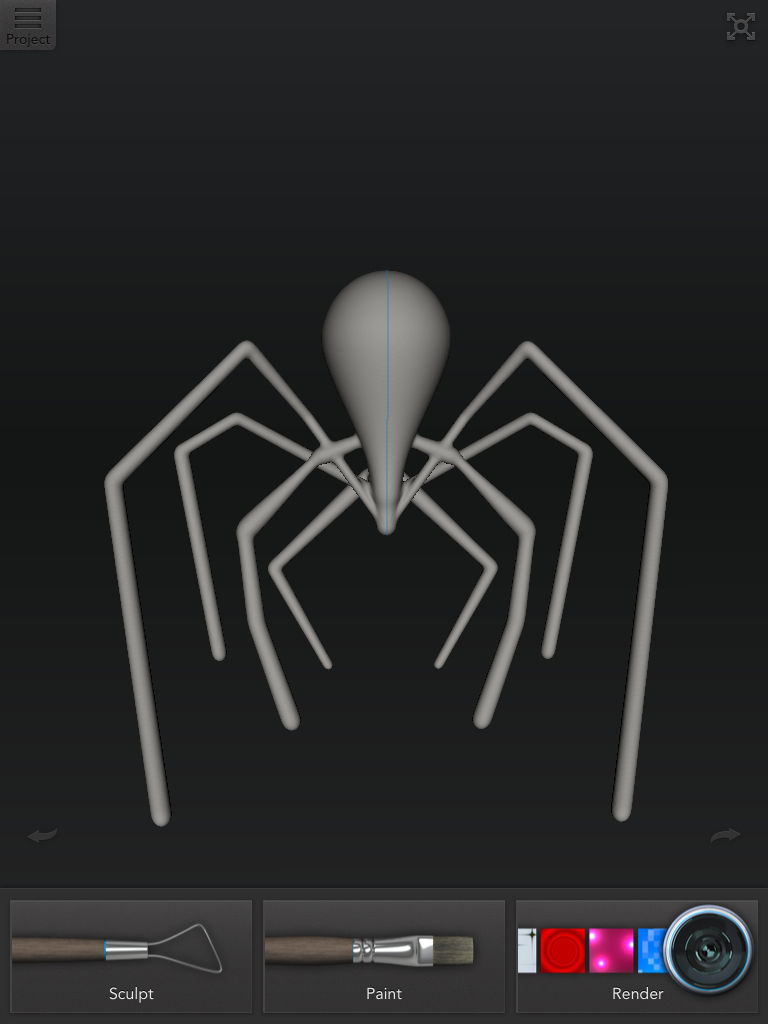


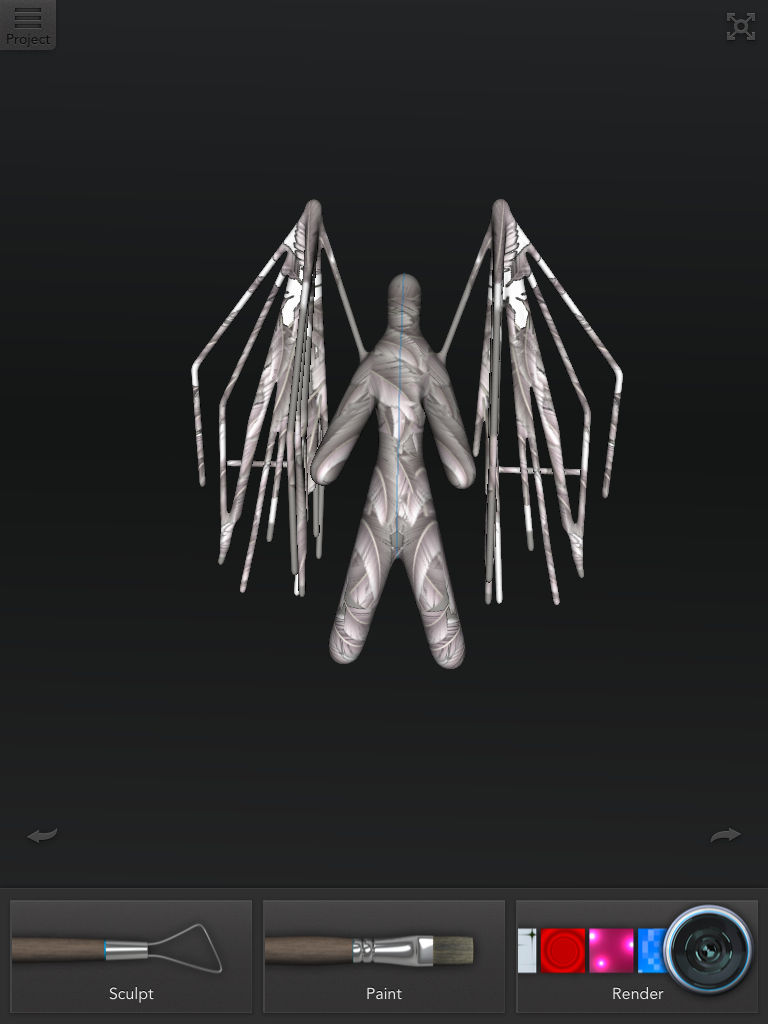
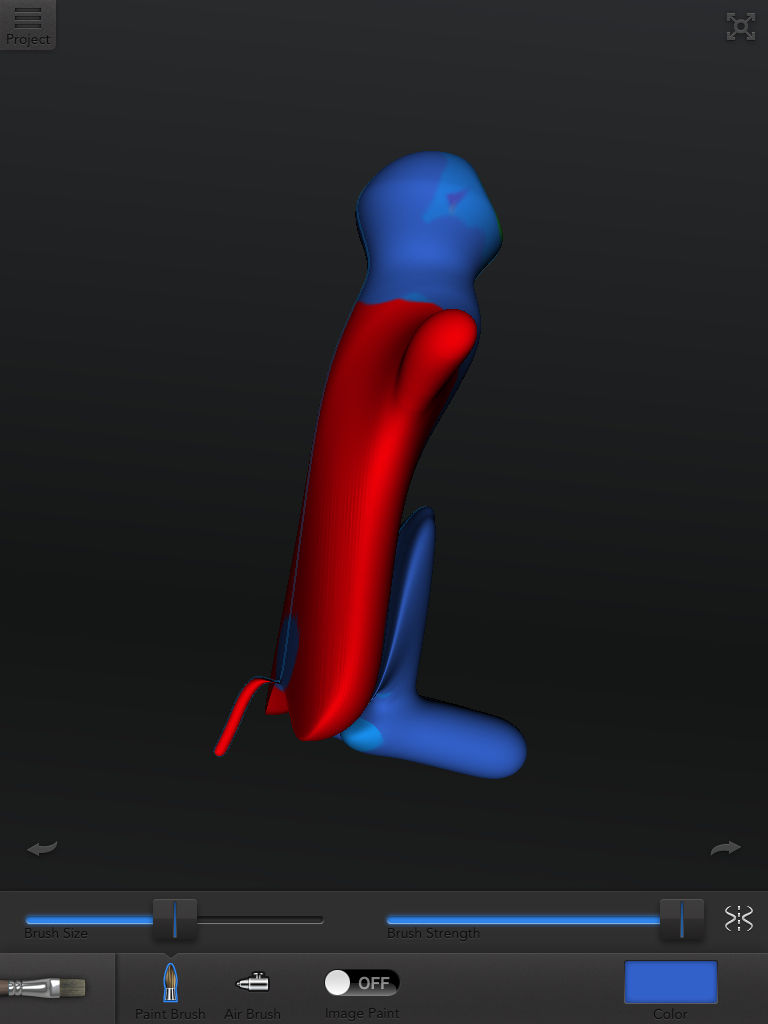


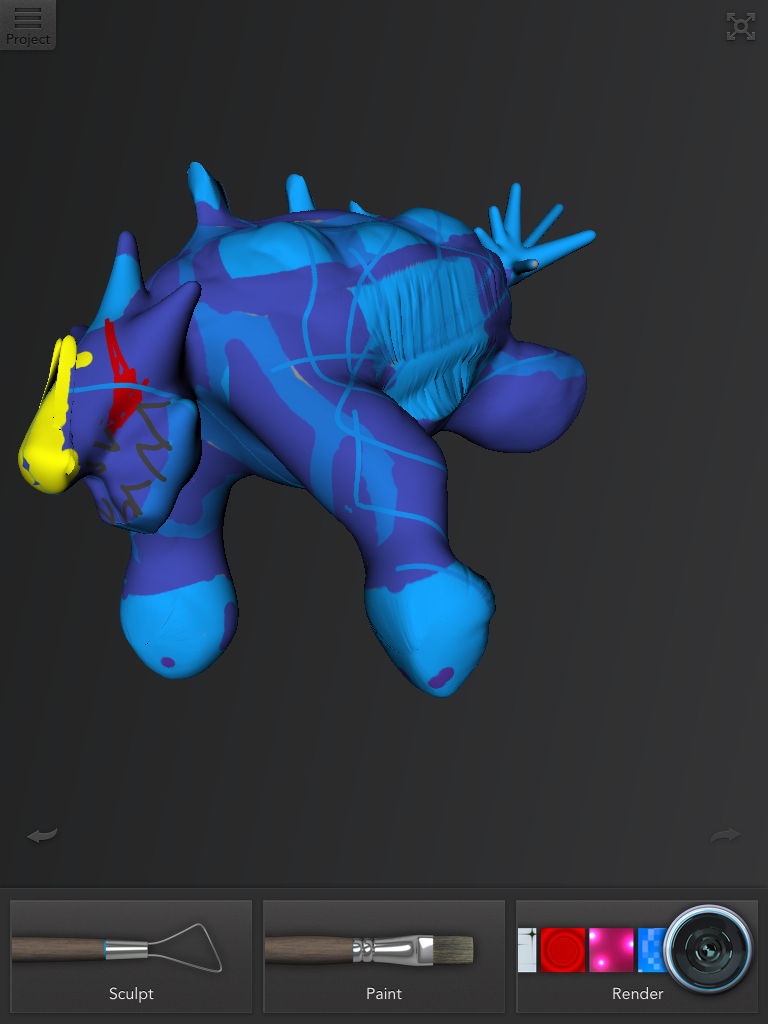



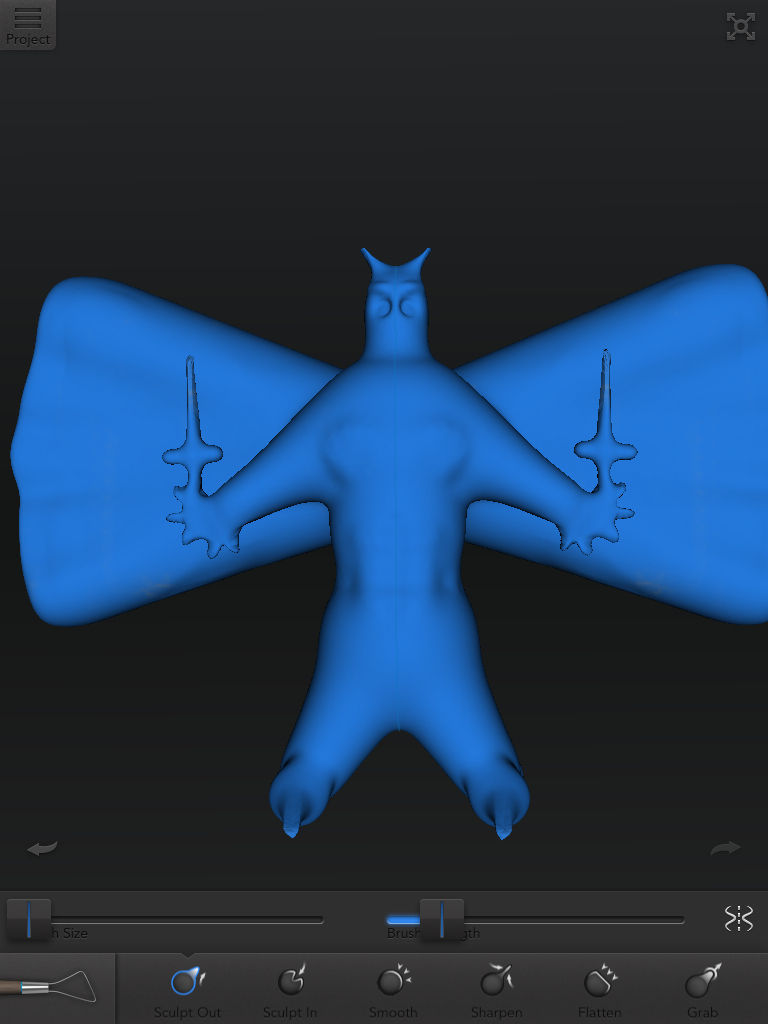

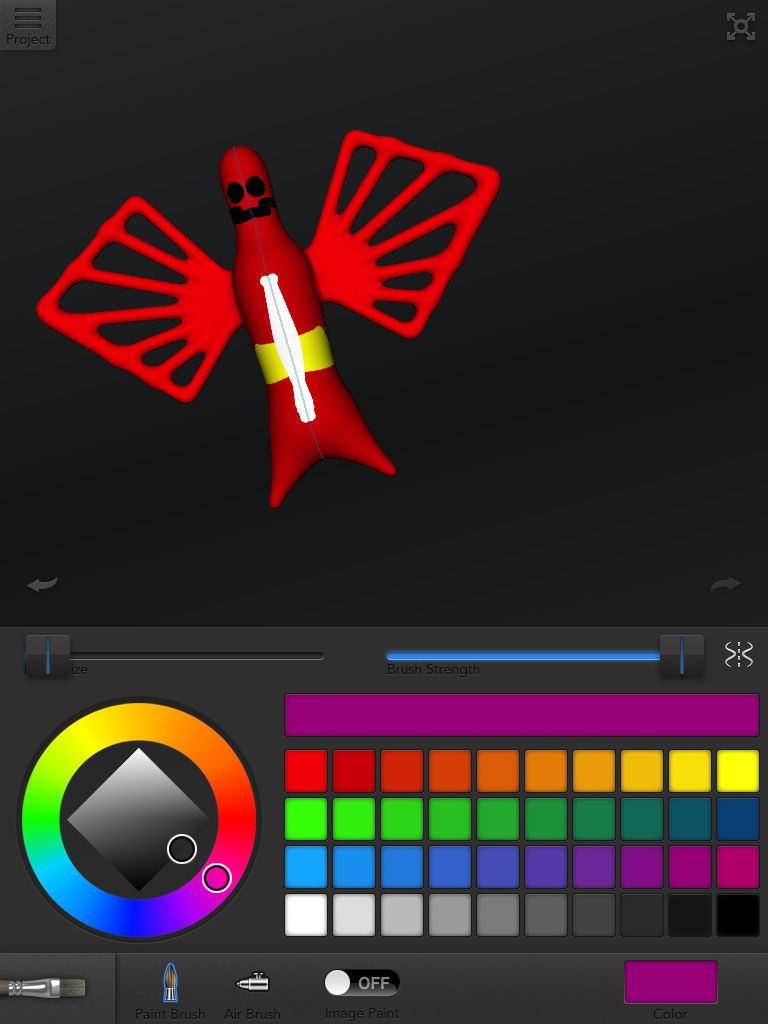


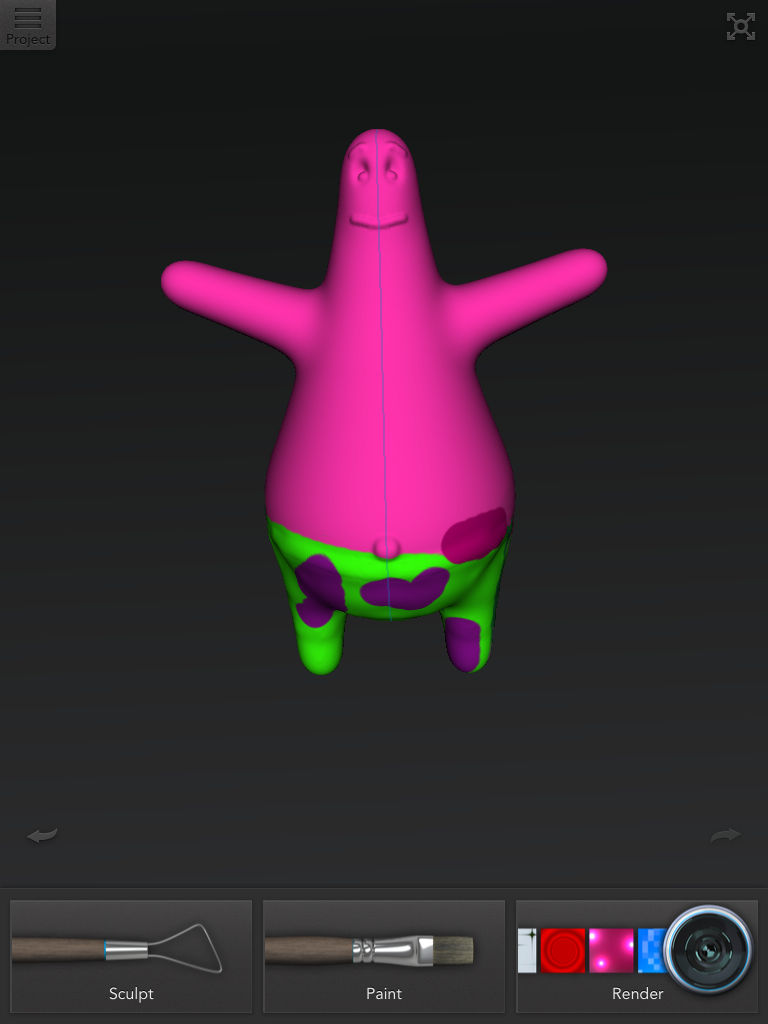
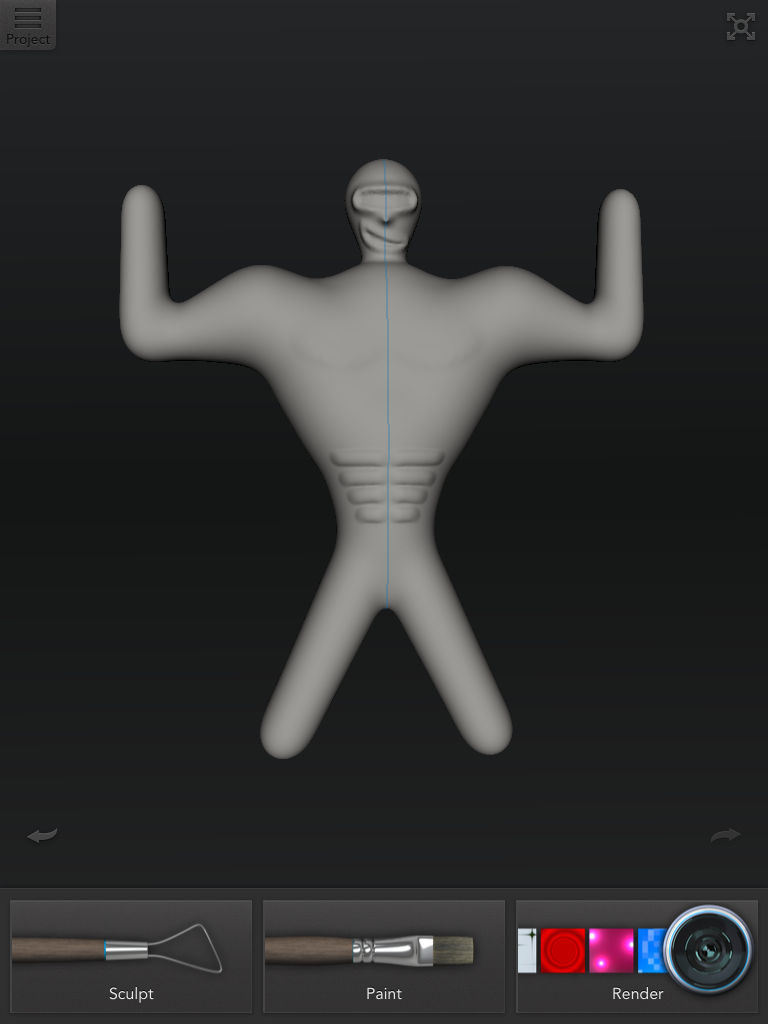
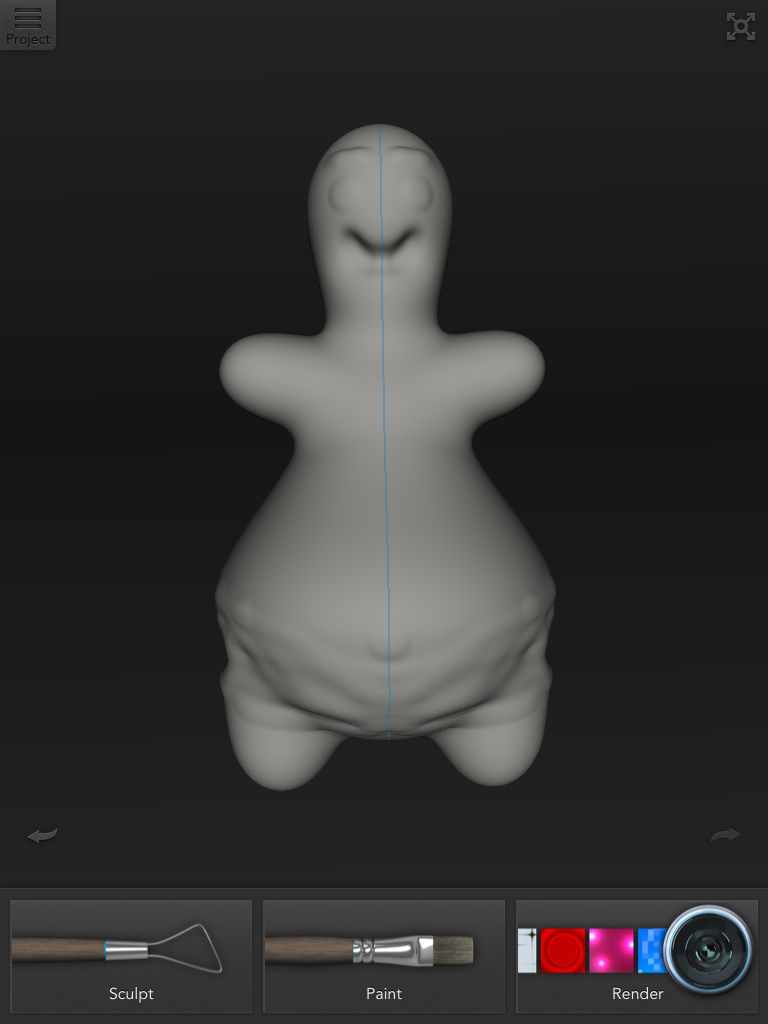




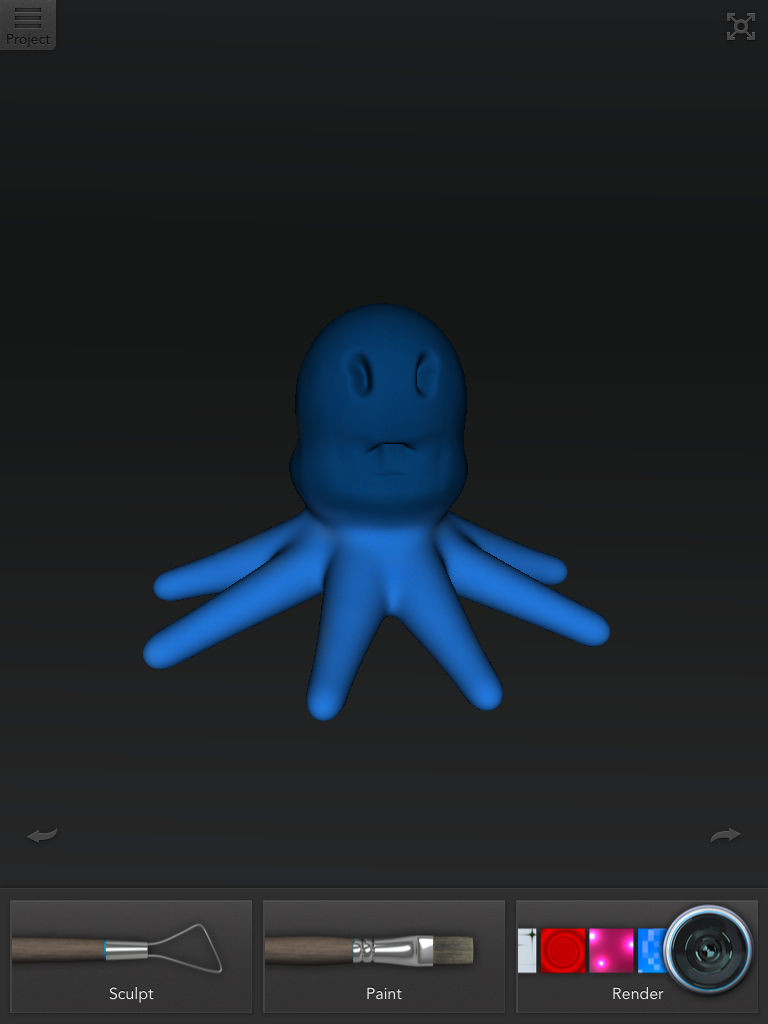
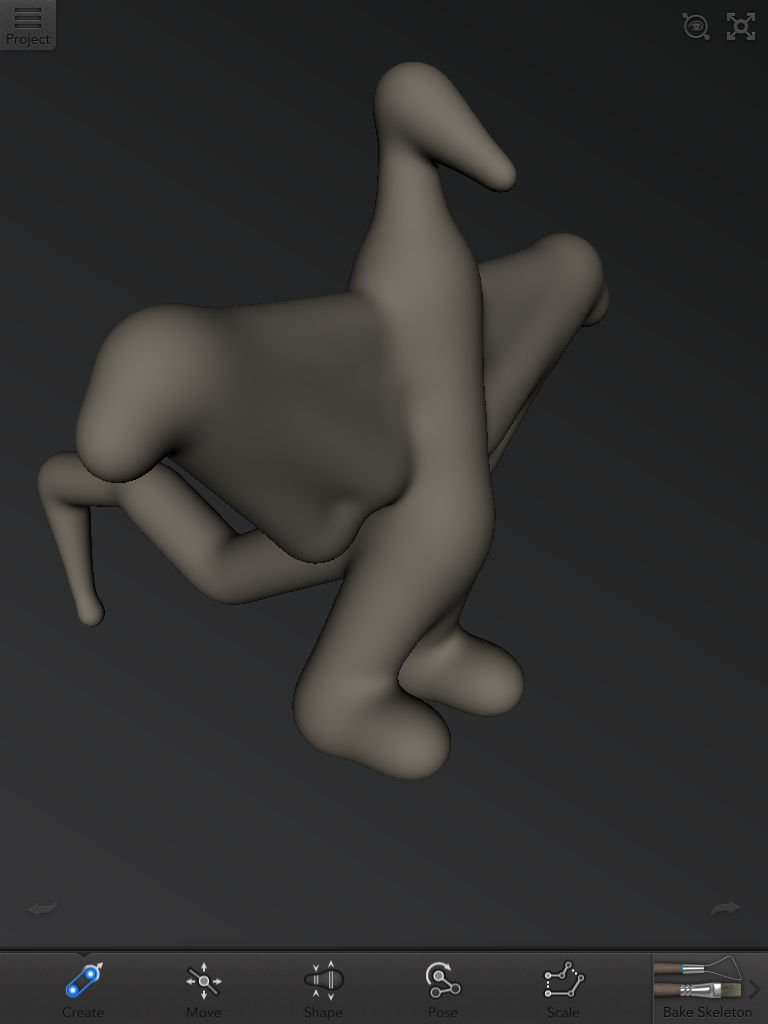
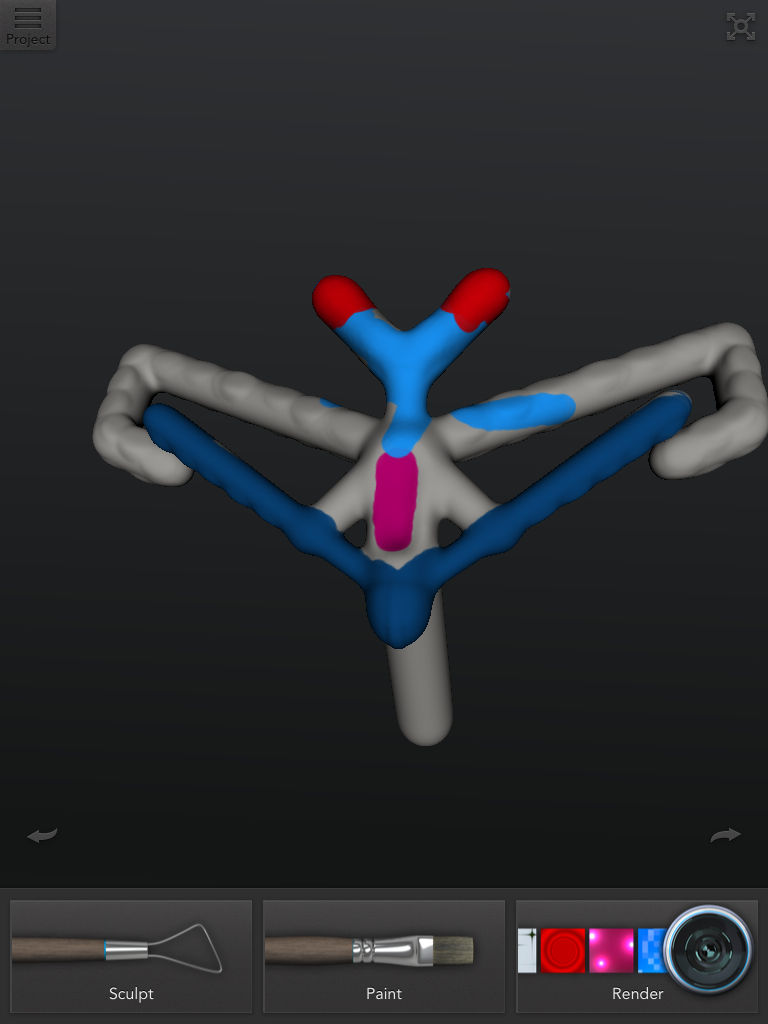

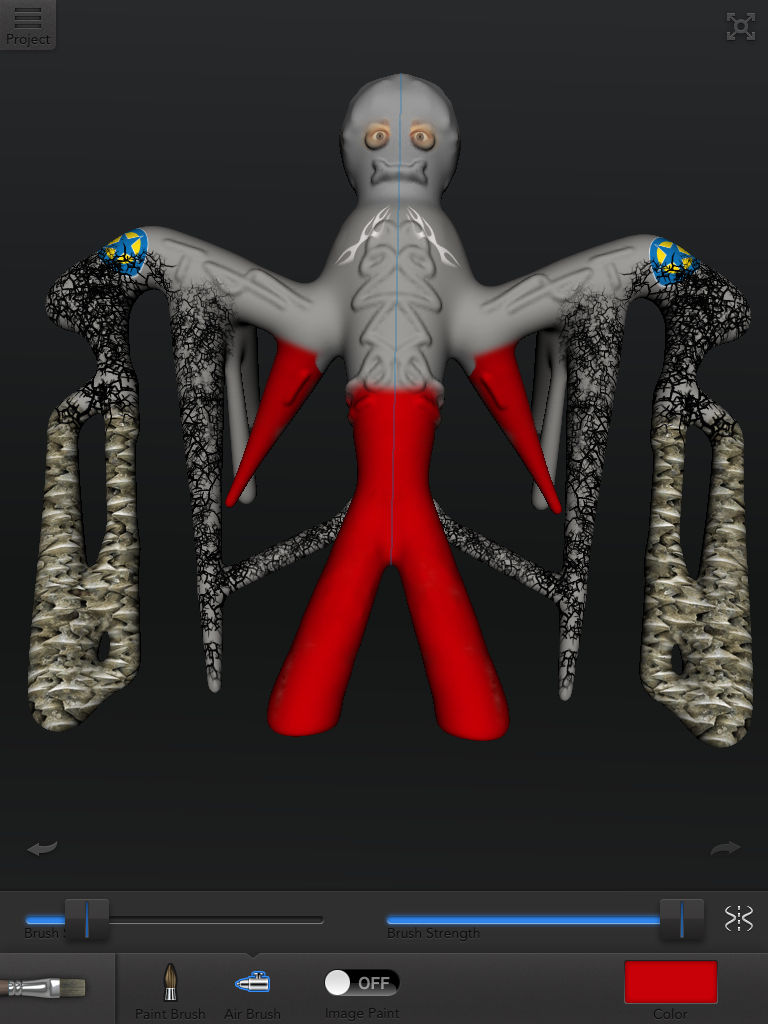

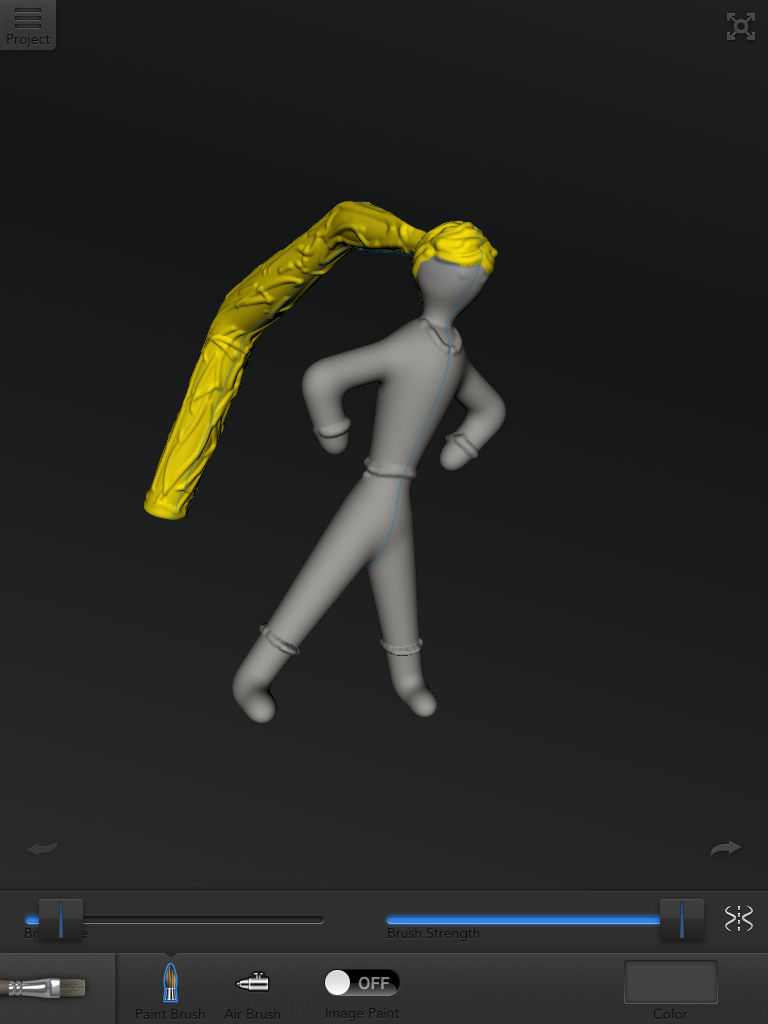


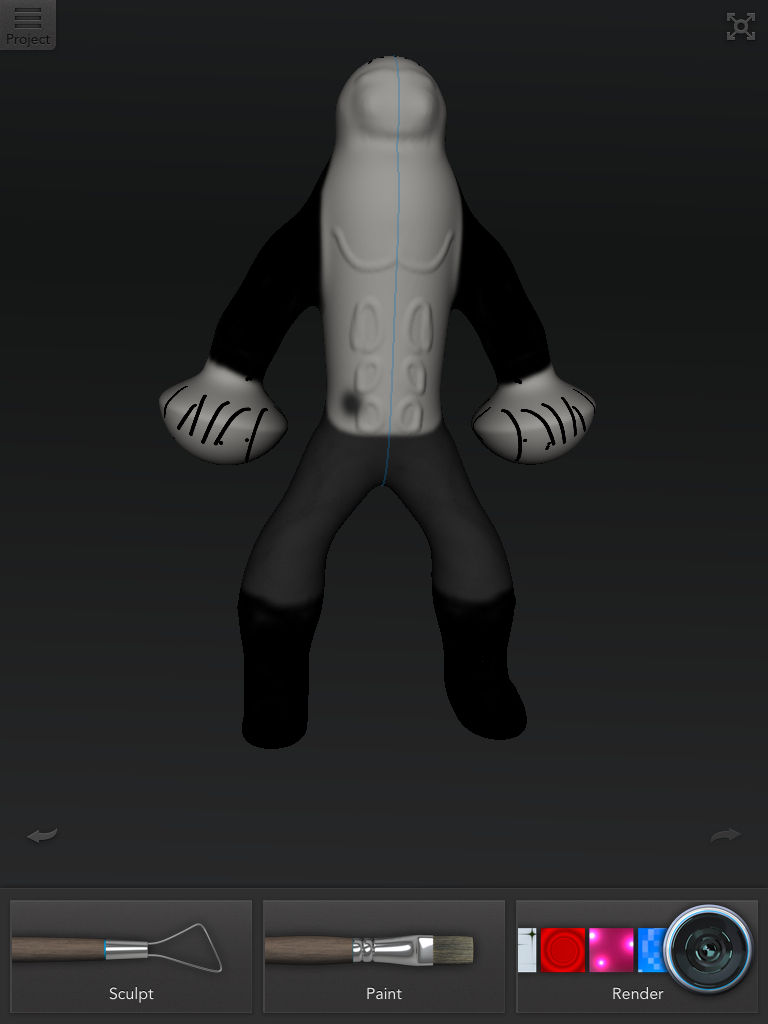


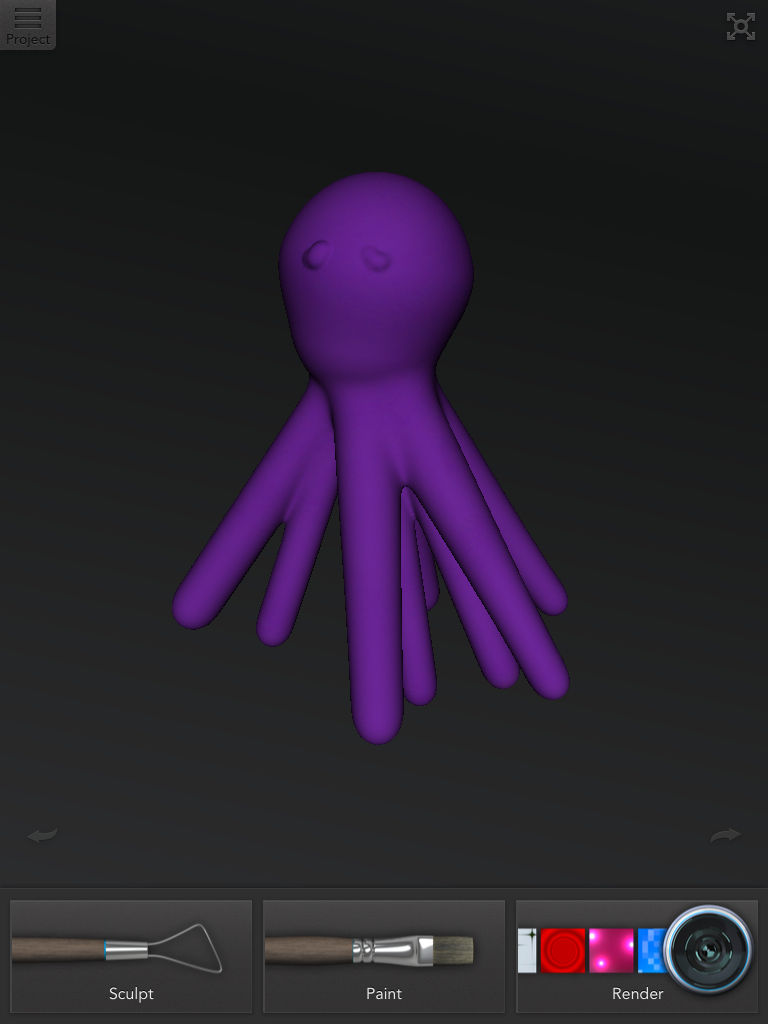


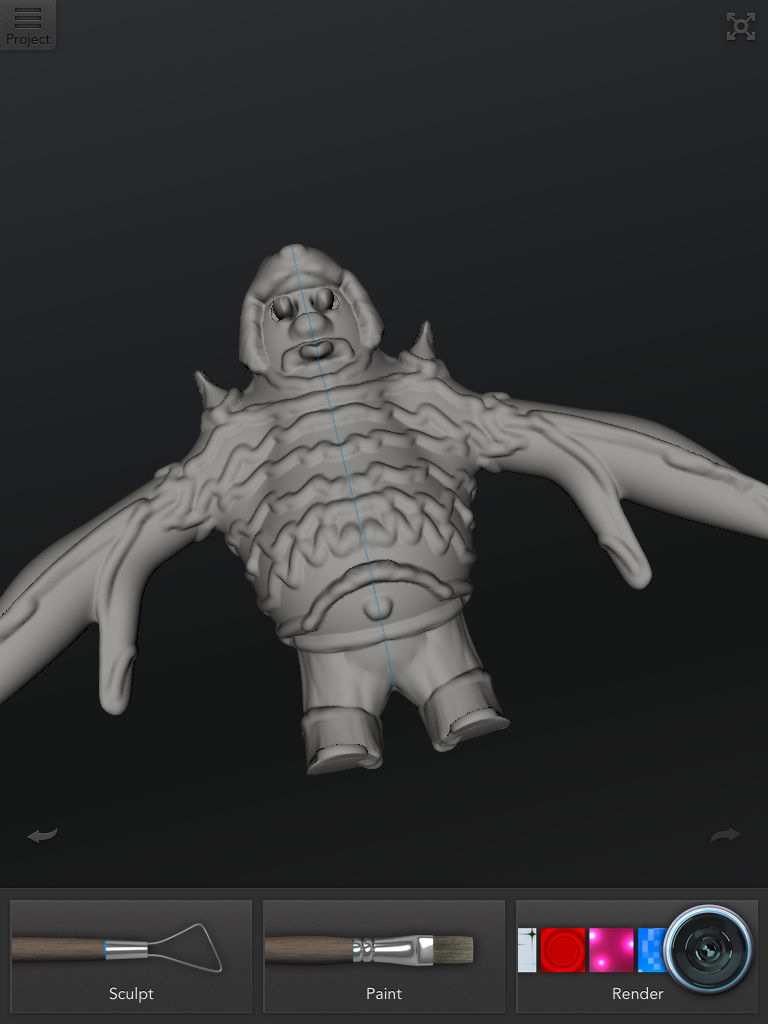

Over the first 2 days the students took part in a 123DCreature iPad lab. 123DCreature is an iPad animation program that let's you plot a 3D character on a graph, you cna change the dimensions of the character with just a sweep of your finger and add detailed features, as well as incorporating colors and patterns.
The focus was on monsters and heros, in the grid below you can see all the creature designs.
These images were then sent to a 3D printer, and made into tangible reality!
For the CAD lamps, the students made their own lamps, and then worked in groups to design the lamp shade using CAD software.



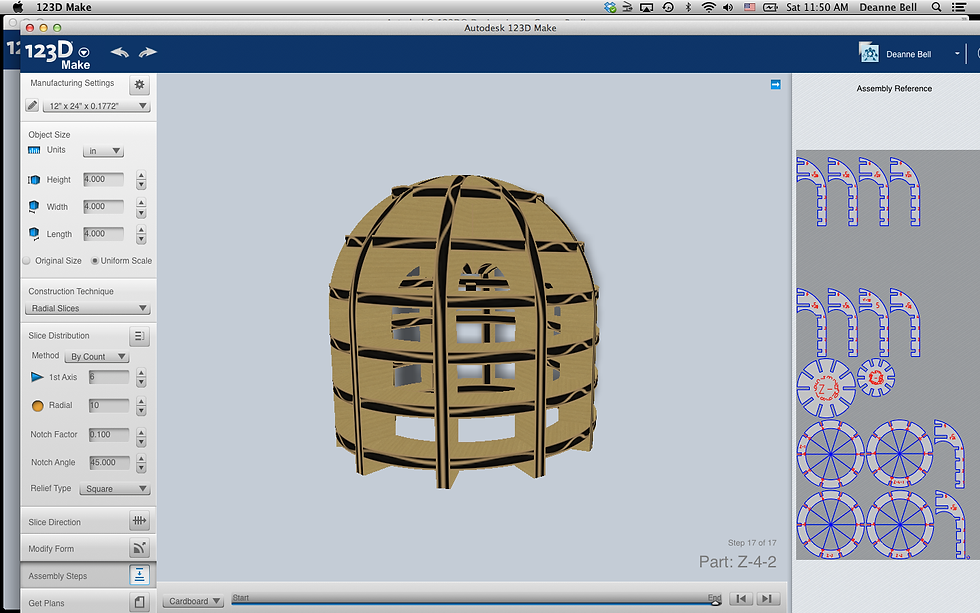
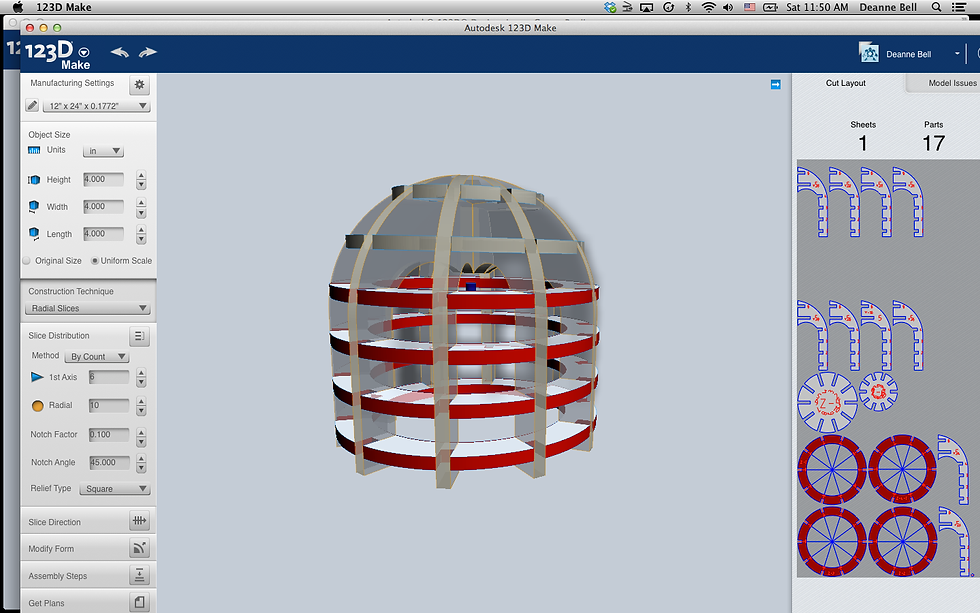
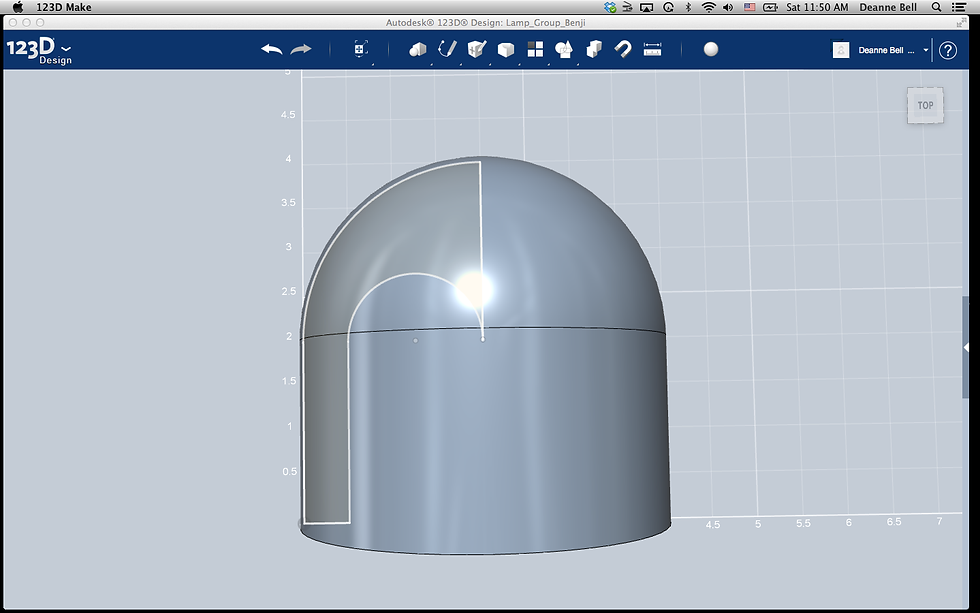



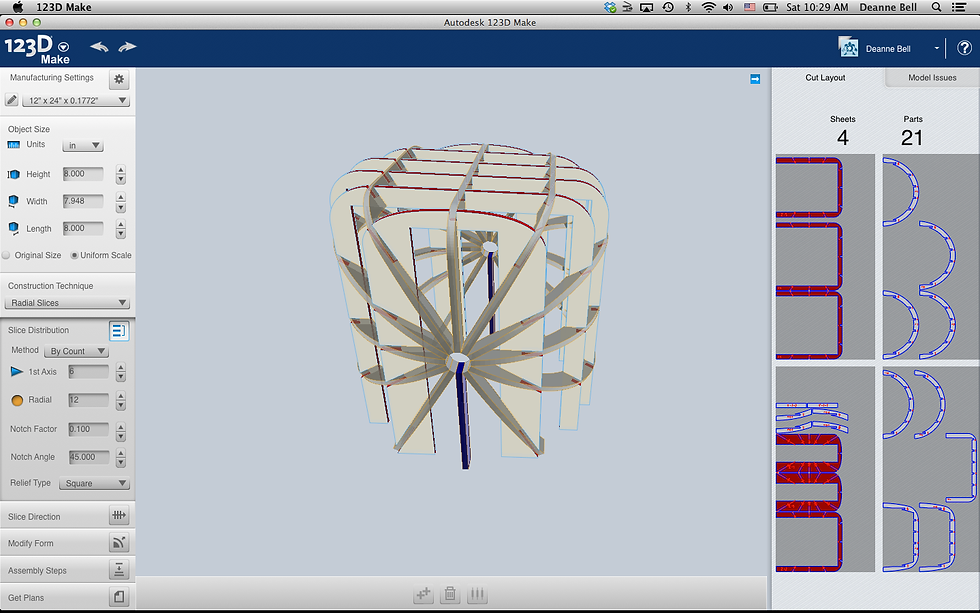


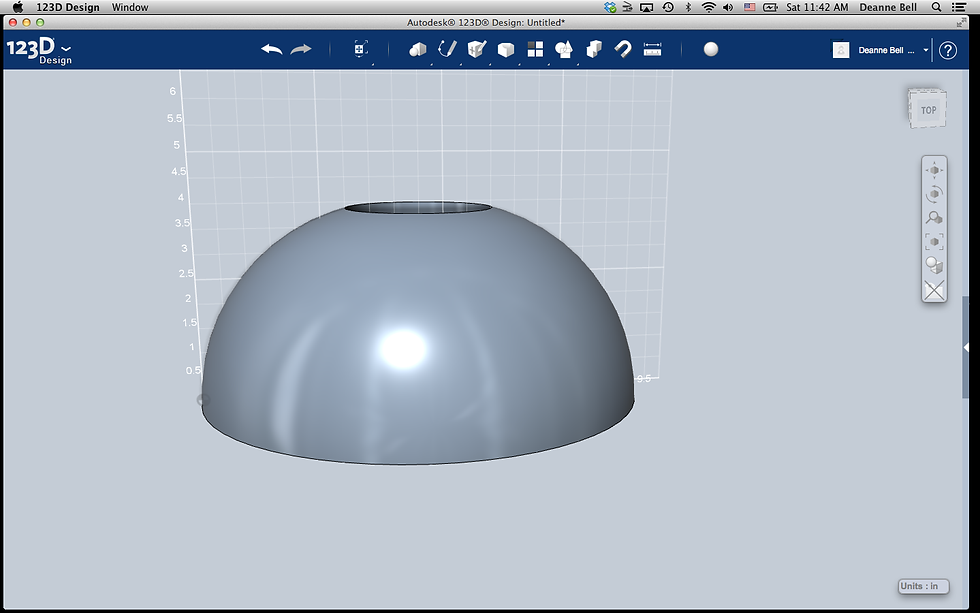





The above gallery shows the lamp shade designs on the CAD software. Below are the finished 3D designs.
The designs were made on day 3, that night Deanne took the designs to be laser cut out of cardboard. Our engineers were then able to put together the lamps first thing the following morning.
Coincedentally that was the same day that Carla Hartman from the Eames furniture group came to visit us, so we were able to use the leftover pieces from the lasercut board to craft chairs with intricate patterns and smooth lines.


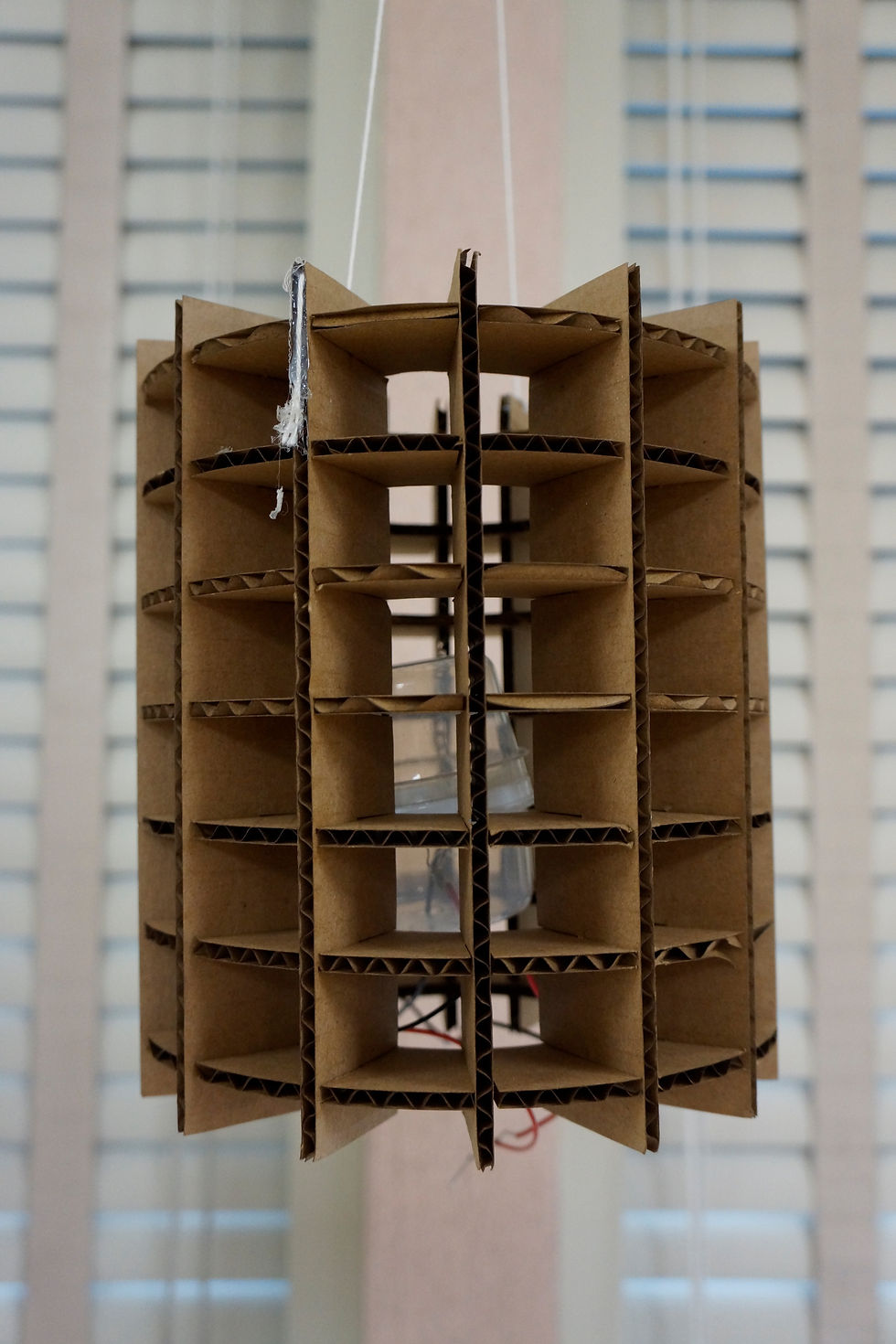

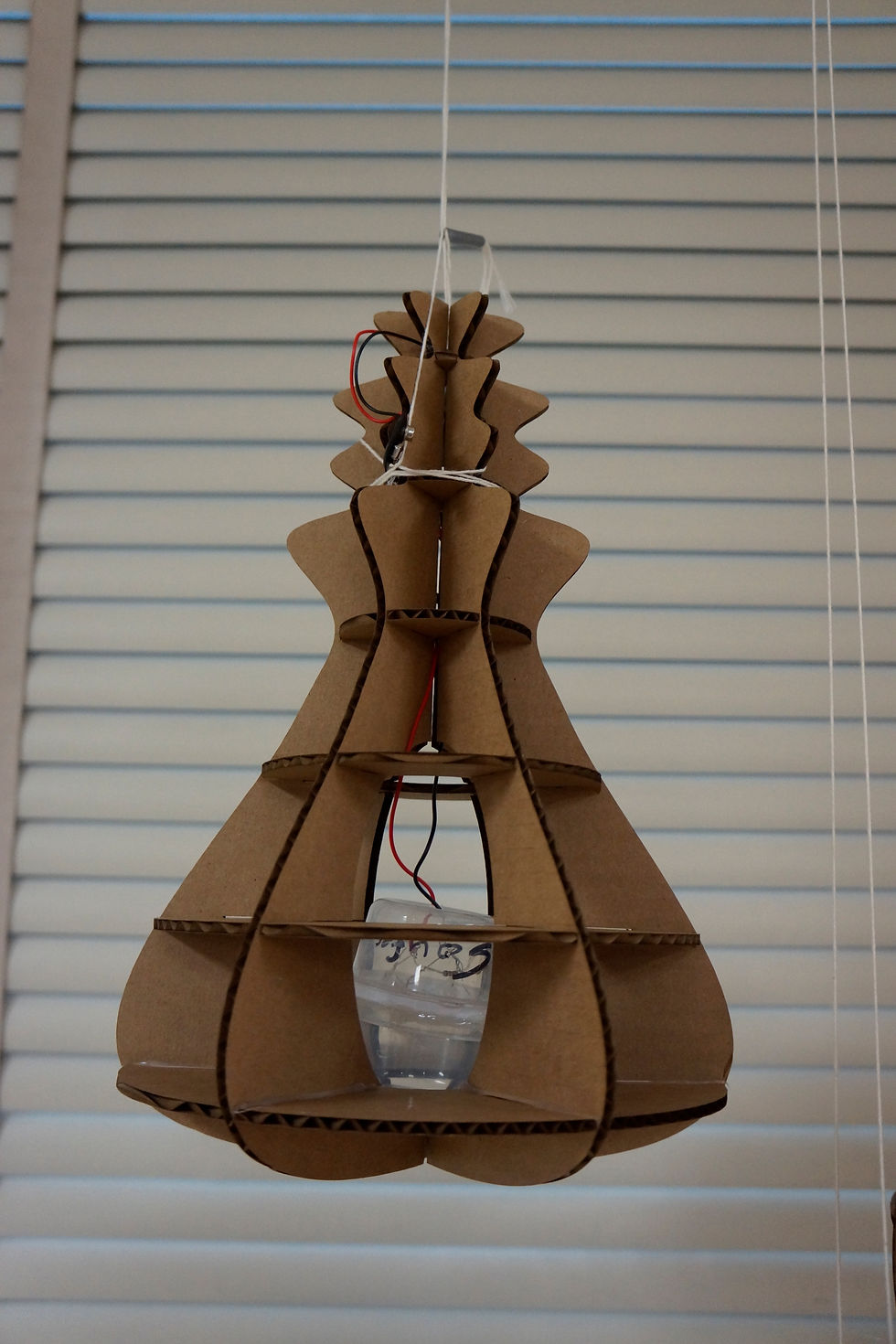







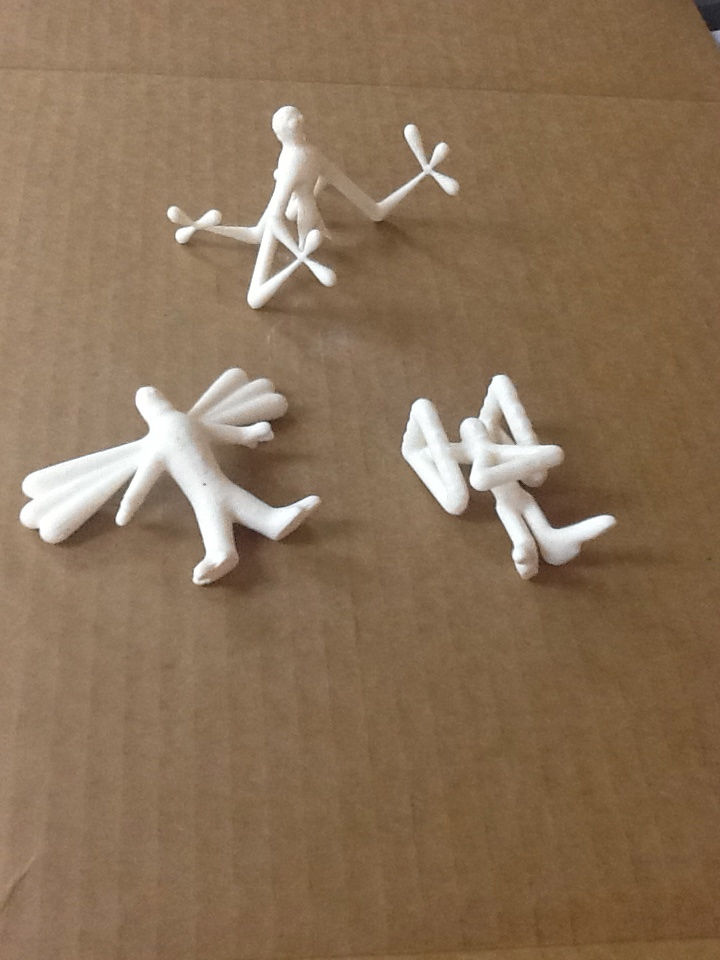
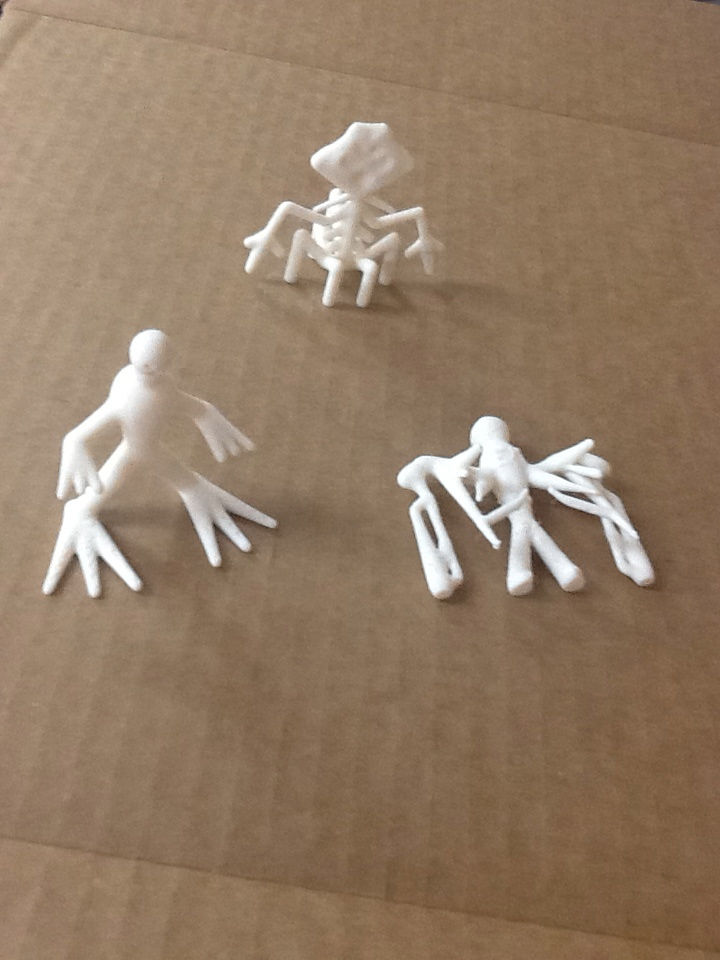
CAD LAMPS!
Automotive Engineering
You know, you can talk about cars as much as you want, wax lyrical on the merits of a manual stickshift and the beauty of a transmission system, but nothing will garner interest in quite the same way as a picture of a really cool looking vehicle. When industrial designer, Jake Loniak, showed us a picture of his invention the Deus Ex Machina, a wearable motorcycle, there was a collective 'Woaaah, that's awesome' around the room.
Jake came in to talk to the group about the future of car design, and the common factors that designers aim for; efficiency and an aerodynamic body. He talked about different sources of inspiration, and pointed out that some cars are supposed to evoke the image of an animal.
With this in mind, the rookie engineers took lumps of clay and sculpted car bodies aiming to minimise air friction, and give them serious style.
Resources:
Title. Double click me.
CAD & Creature Design: http://www.123dapp.com
Creature Prep: http://www.makerbot.com/blog/2013/03/05/step-by-step-for-123d-creature/
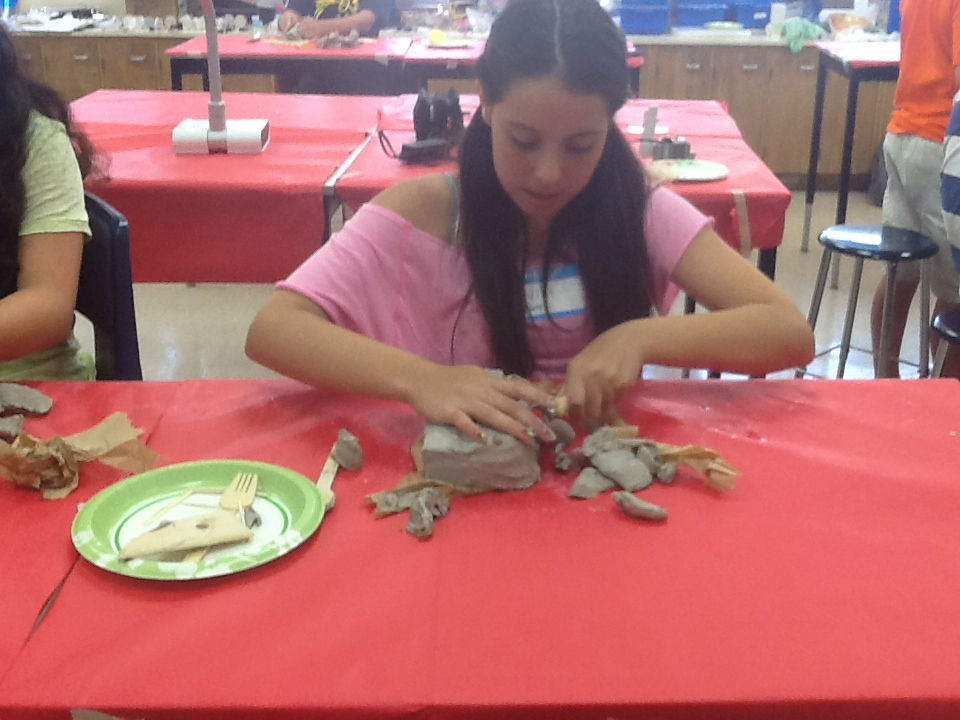
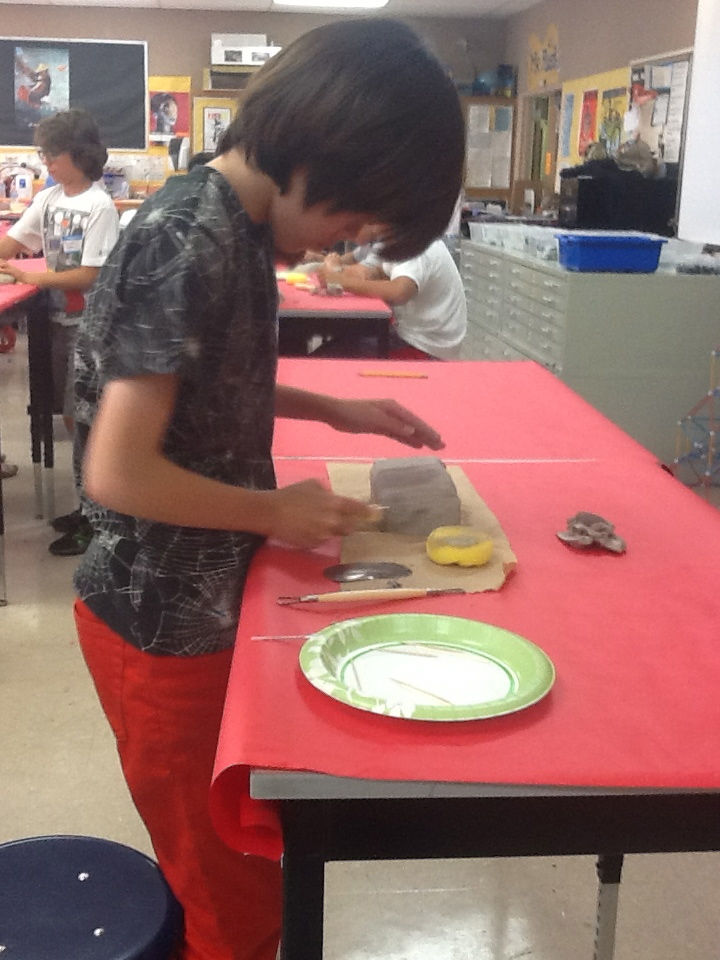
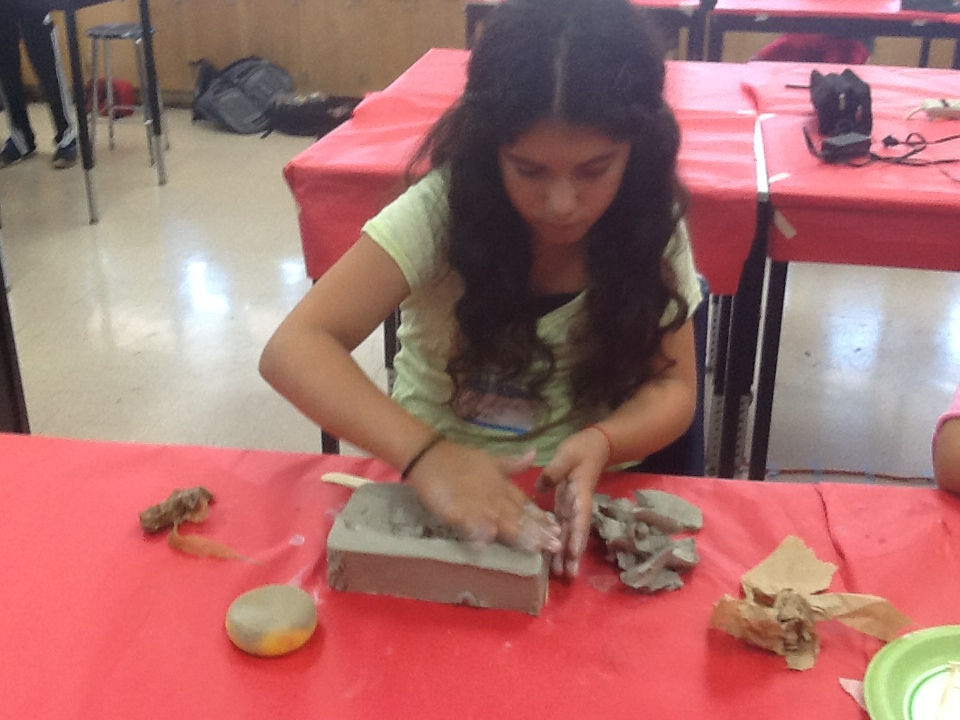

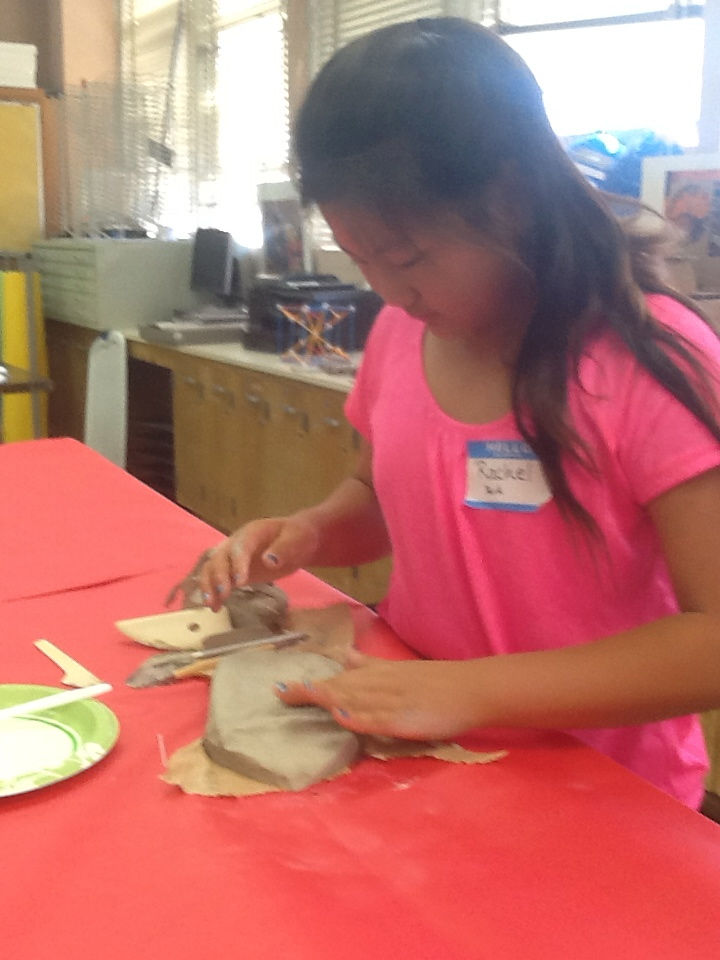


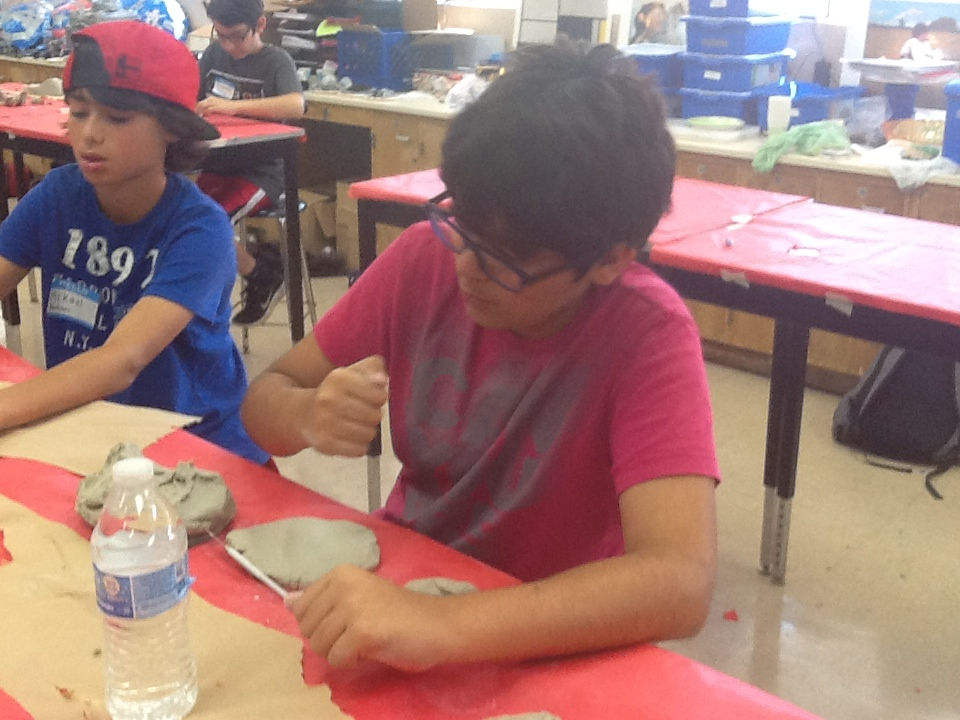


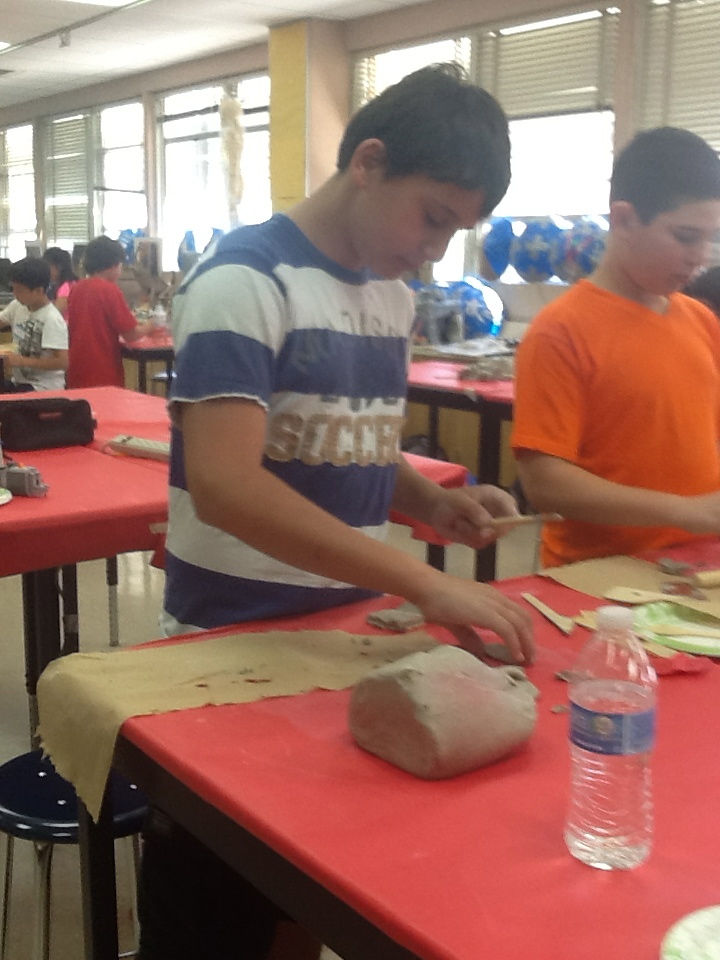
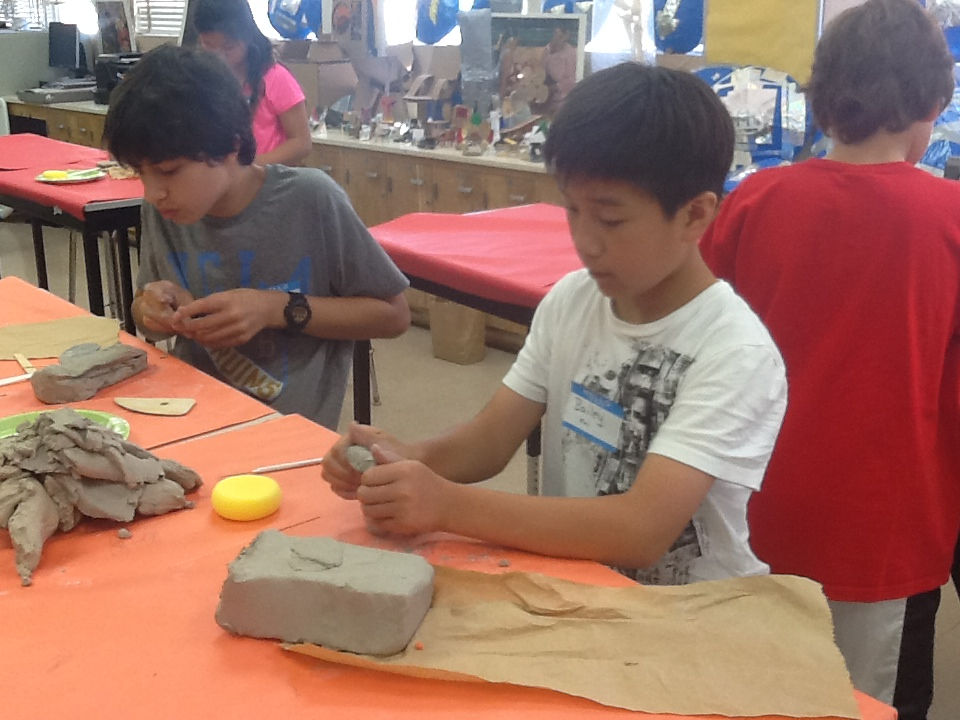


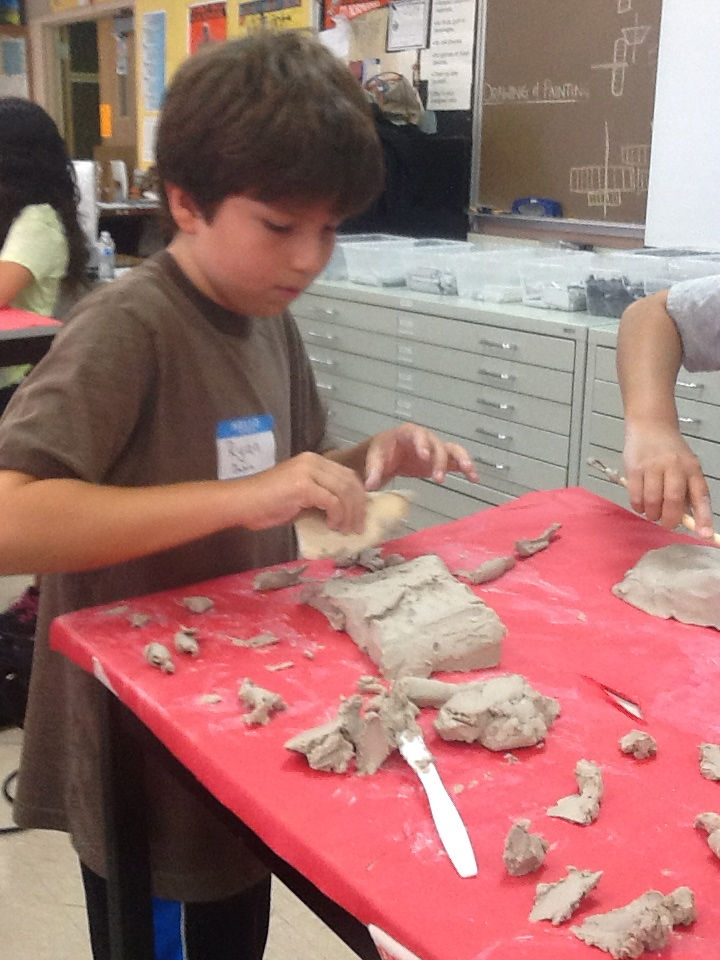
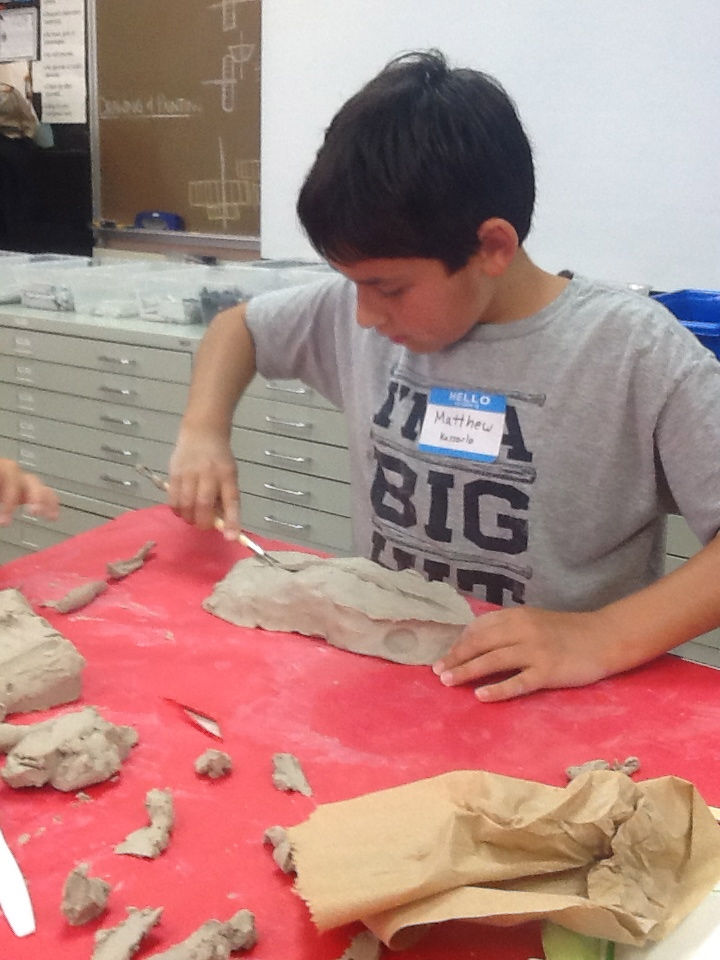




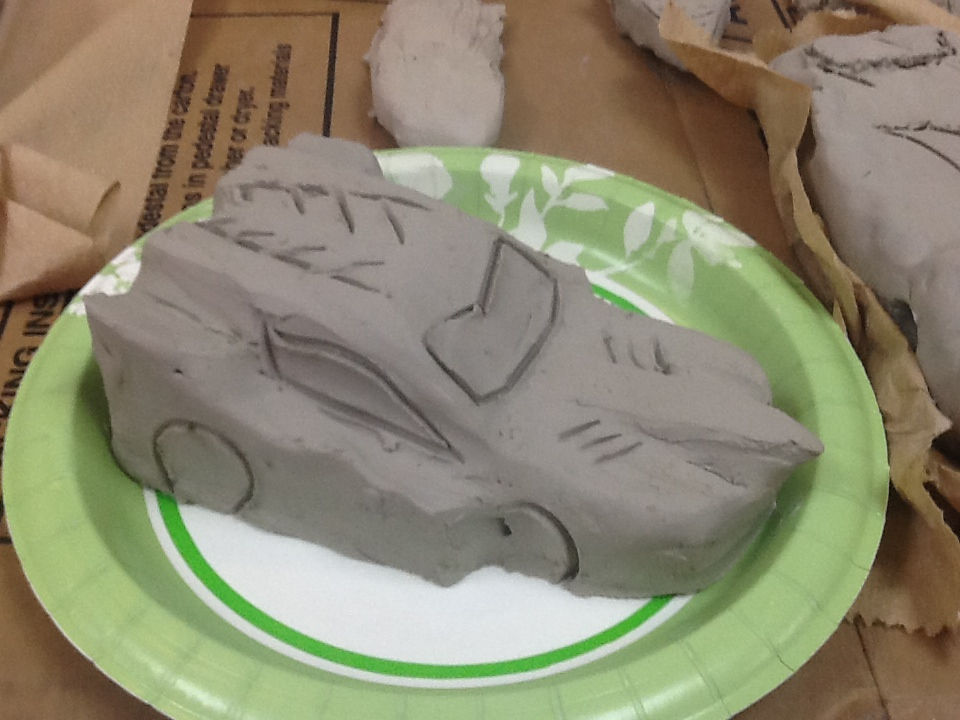
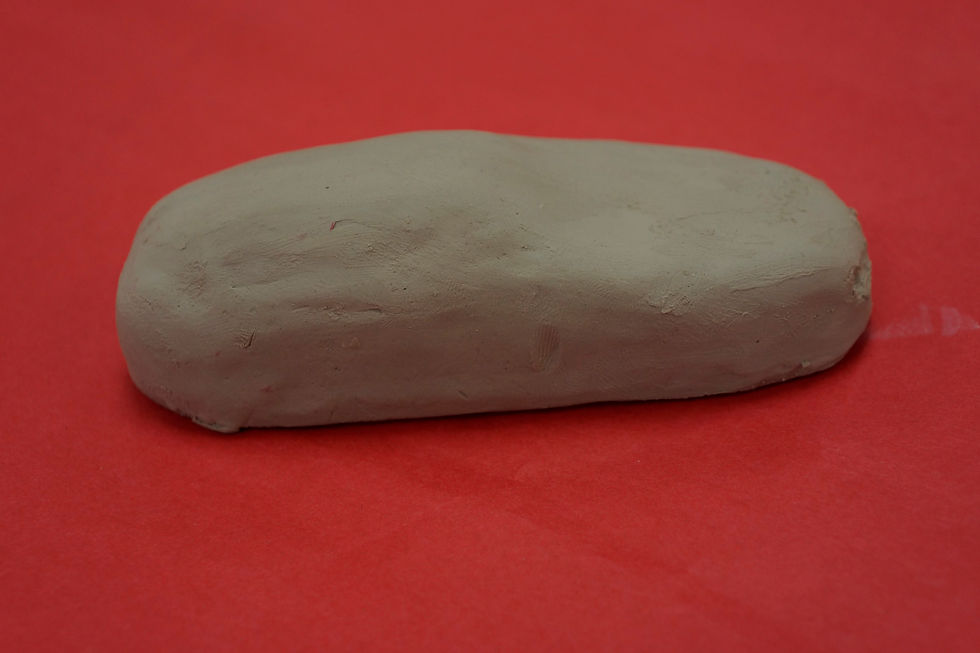




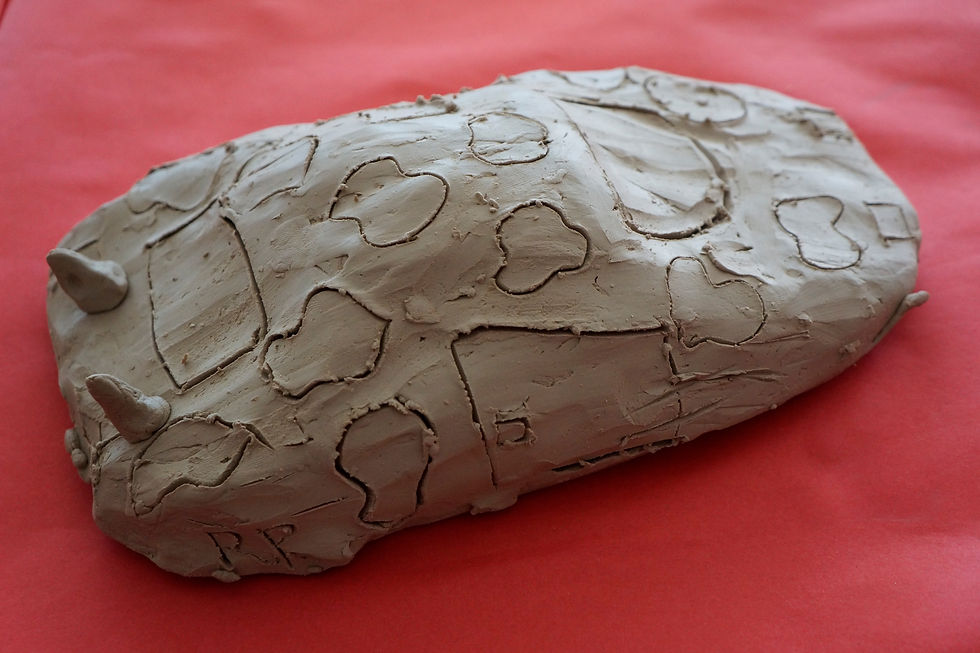

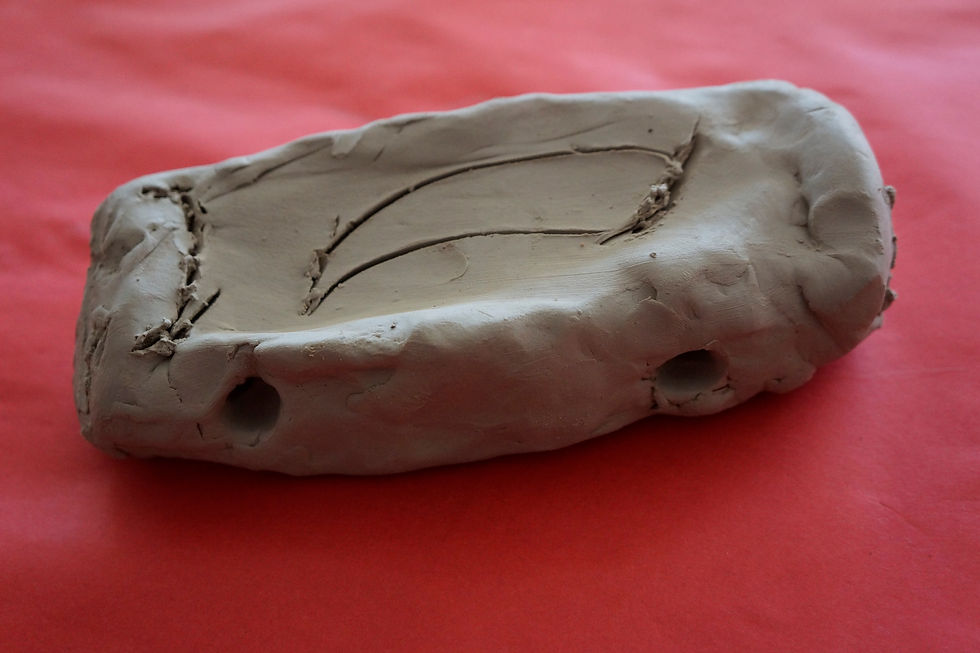


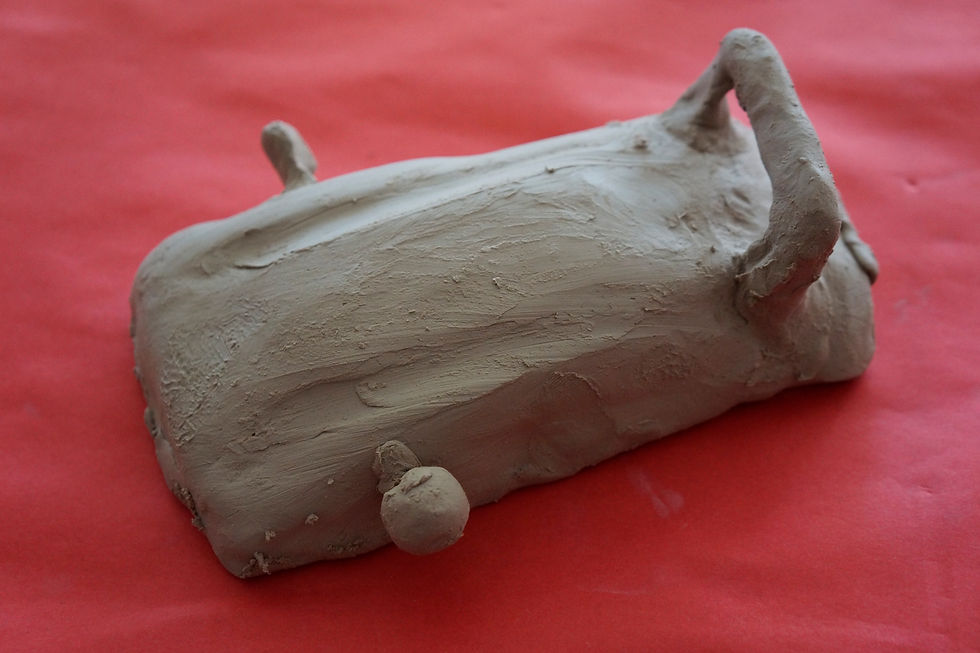
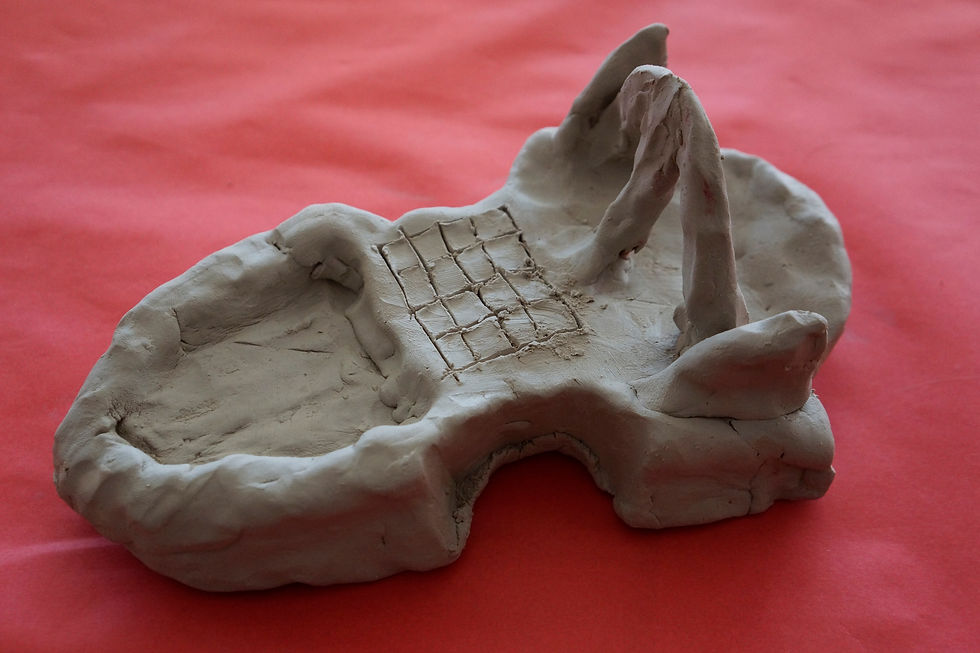
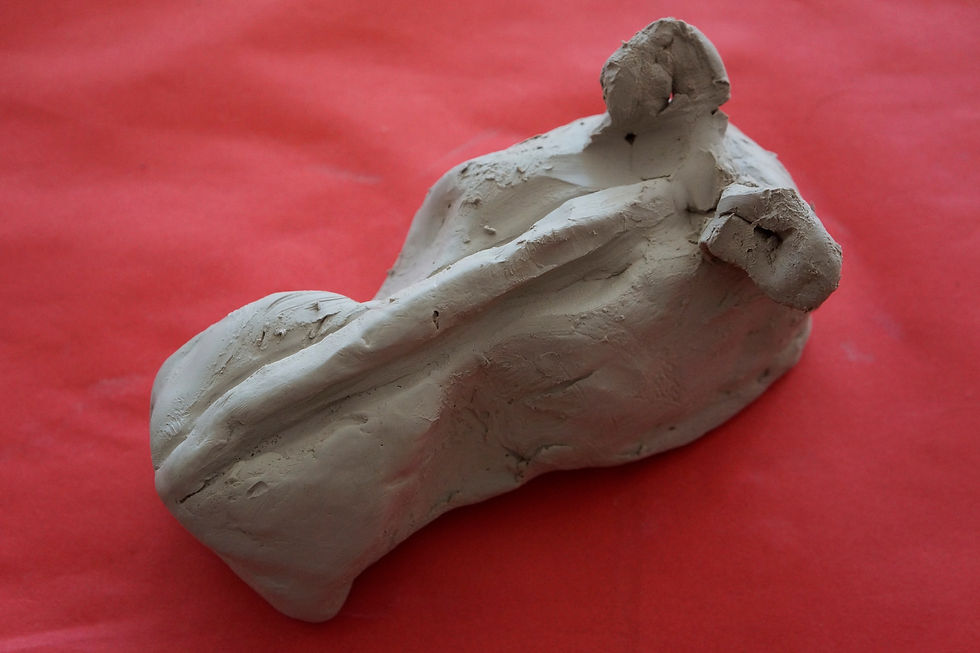
In order to understandhow the inside of a car works we turned to legos!
The students used specific lego pieces to learn about gear trains and power transmission, they figured out how to 'gear up' and 'gear down' to either make a car go faster or to give it more power.
They used their knowledge to design two working vehicles, one built for strength and the other for speed, and then put their cars through challenges to test them, a weight pull and a some good old fashioned racing.


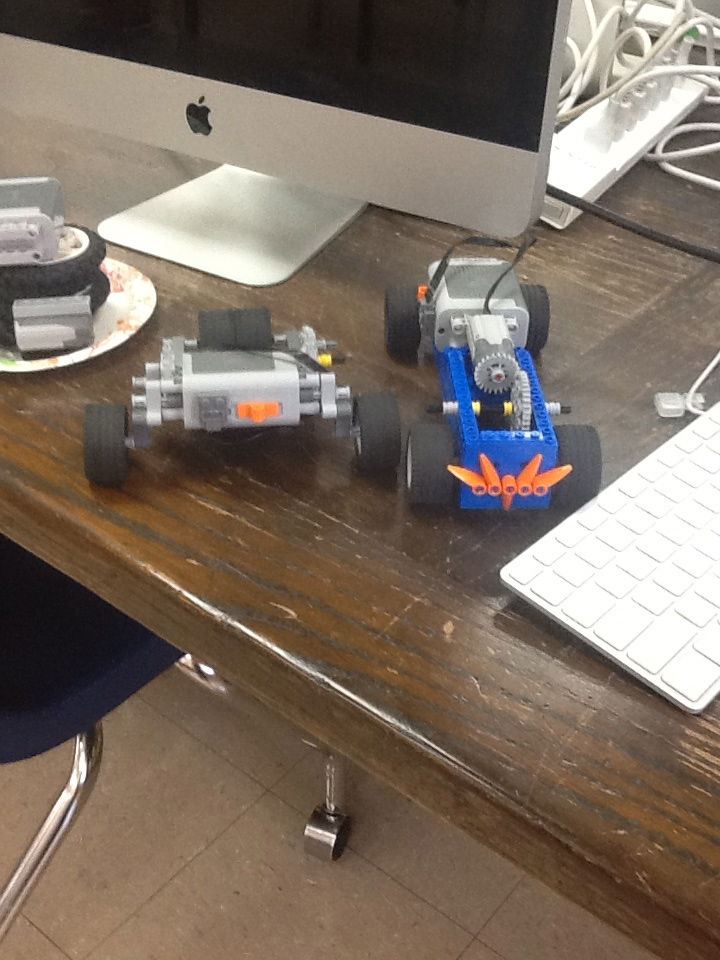

Here Come the Robots!
After figuring out how to make a moving automobile, our engineers built on that knowledge to make programmable robotic vehicles. For this we used the Lego Mindset line. These contain a 2" x 3" 'brain' and various sensors - light, color, sound, and movement - as well as various lego pieces to create a mobile platform and make the body of your robot. The idea is that you program the functions and sensor responses of the robot on a computer, and then download the program into the 'brain', which is then wired to the sensors on the robot. Sounds simple, but it proved fiendishly difficult!
Our robots design requirements were that they had to be able to complete an obstacle course: following lines, avoiding 'minefields', performing set funtions and successfully moving a cup full of marbles.
The programming called for meticulous precision in terms of distance and timing, and our robotics teams spent hours testing, re-callibrating, testing again and going back to the drawing board to make those teeny tiny adjustments that lead to perfection.
And of course this was day when we had the man from NASA bringing a mini-Mars Rover to see us!!
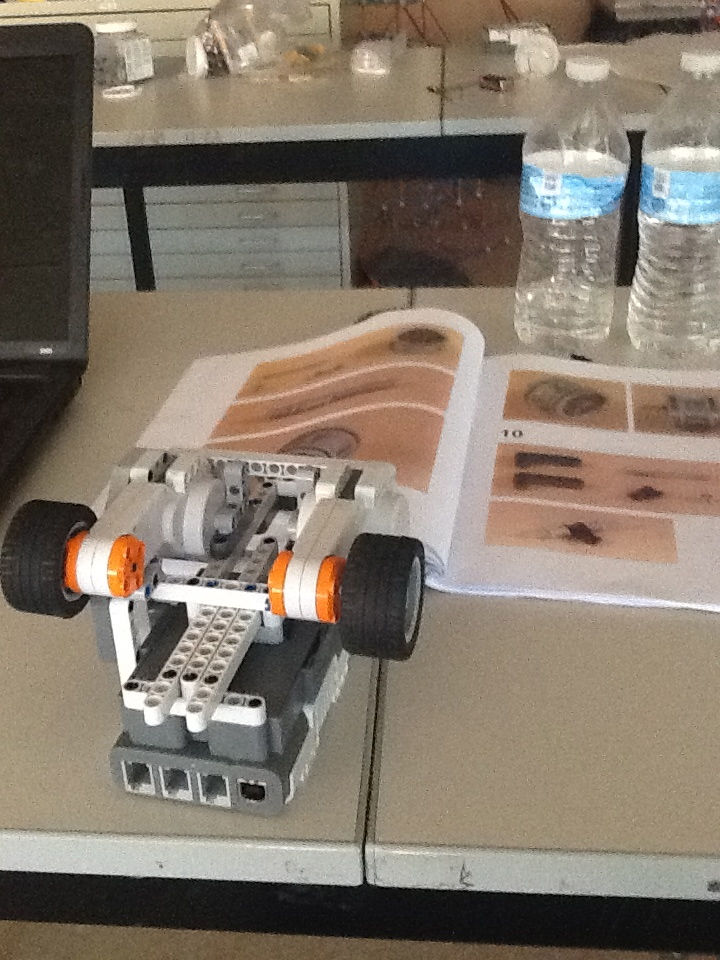


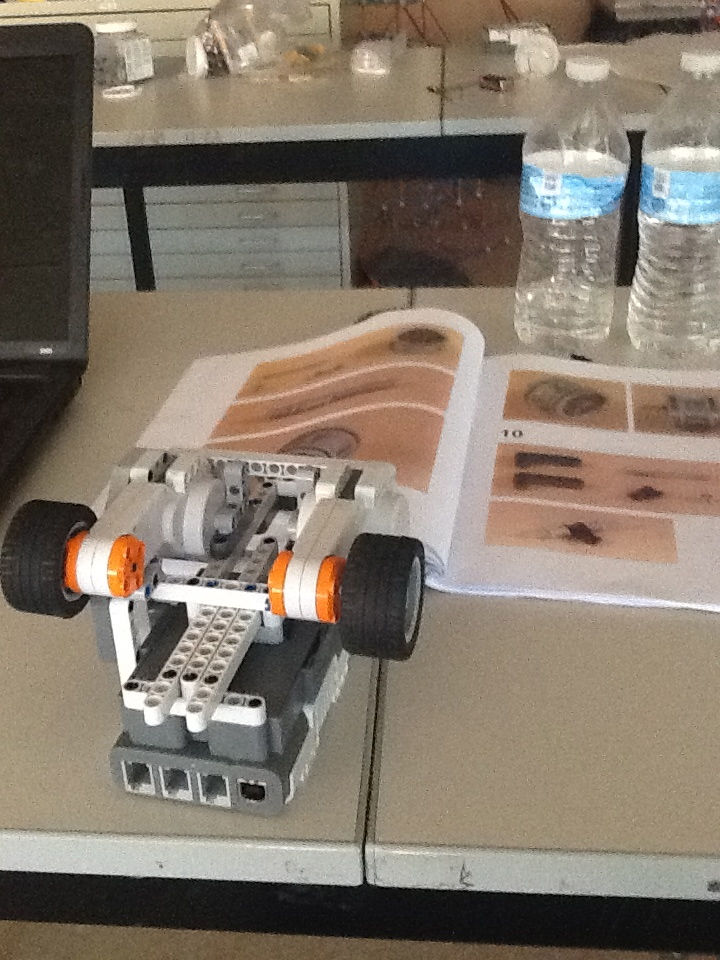
.It's Here!!
THE RUBE GOLDBERG CHALLENGE!!!!
'Two and a half days of utter insanity' might not be the best way to describe this challenge, but it's pretty accurate. Dominos, marbles and ping bong balls everywhere. Every construction was either welded together with hot glue guns, or duct taped into oblivion.
To make sure that everyone knew the sky was the limit we showed all the kids the recent OK GO music video which took three months to make and is five minutes of Rube Goldberg Mechanism magnificence, complete with an exploding piano!
Whilst we didn't have a piano to explode, we did have 21 engineers and 220 square feet of space to play with. Because this was such a huge team working on a project we had the students work in teams of 3 or 4 people, at table stations around the room. Each of those stations was further into 4 areas. In this way we were able to have each engineer responsible for one particular area as well as being able to give input to the rest of the team. To get that many people to collaborate successfully was an amazing triumph! We're so proud of everyone.
Each team was designated a place on their area where their mechanism would connect with team's mechanism before them and the next team's mechanism. We also issued 1 challenge per table at their starting/finishing point e.g. "Must start with a collapsing tower", and decreed that every team must have at least one robotic component.
We tested and tested and tested and tested... and then we tested it a whole lot more!




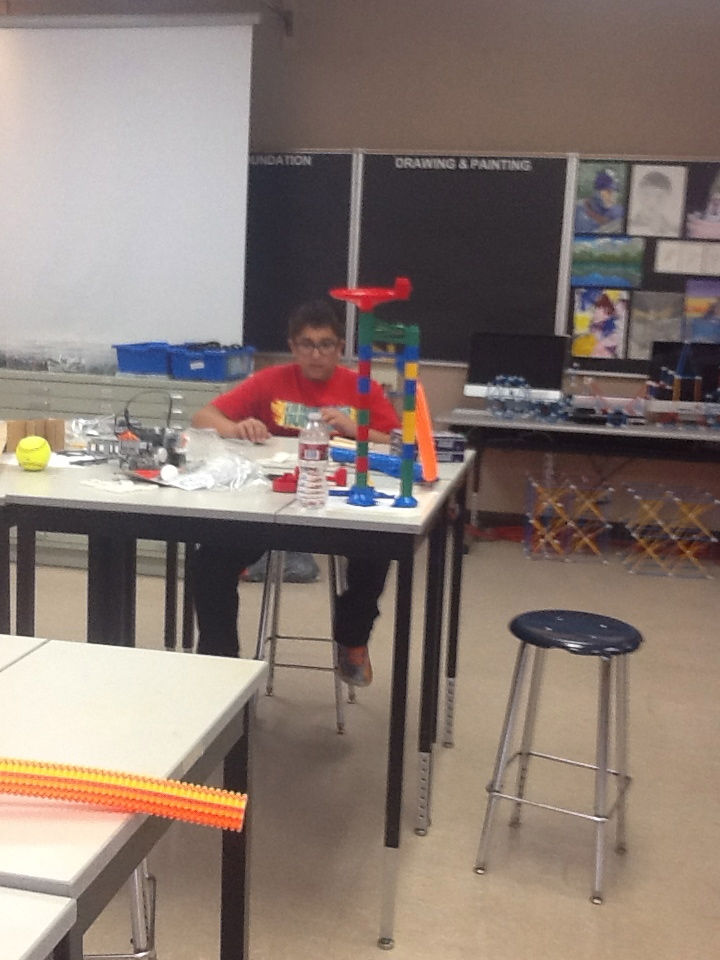


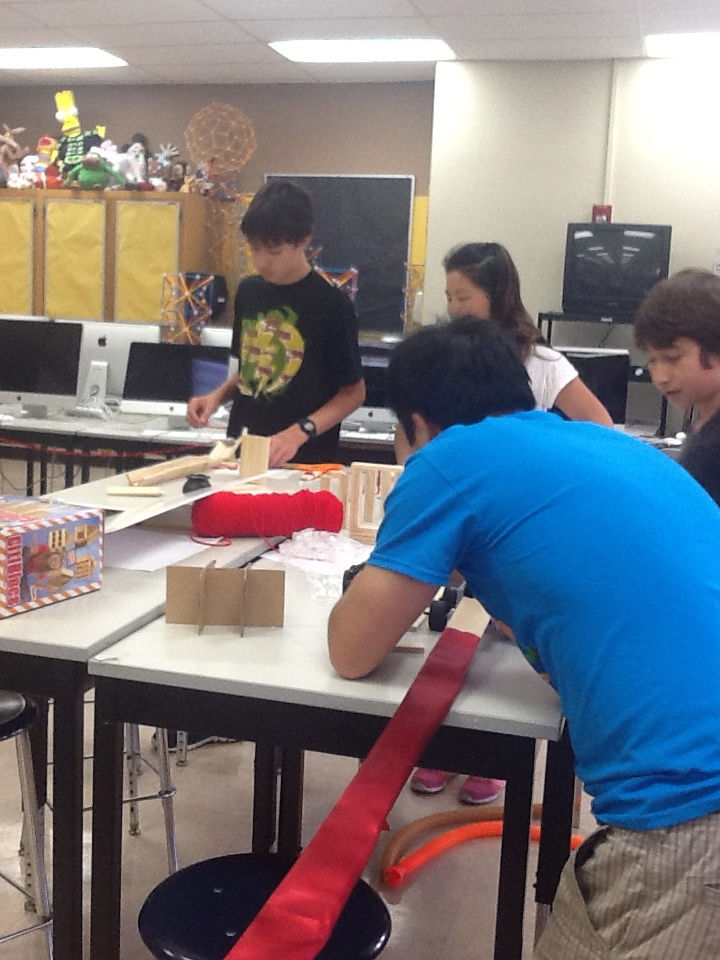






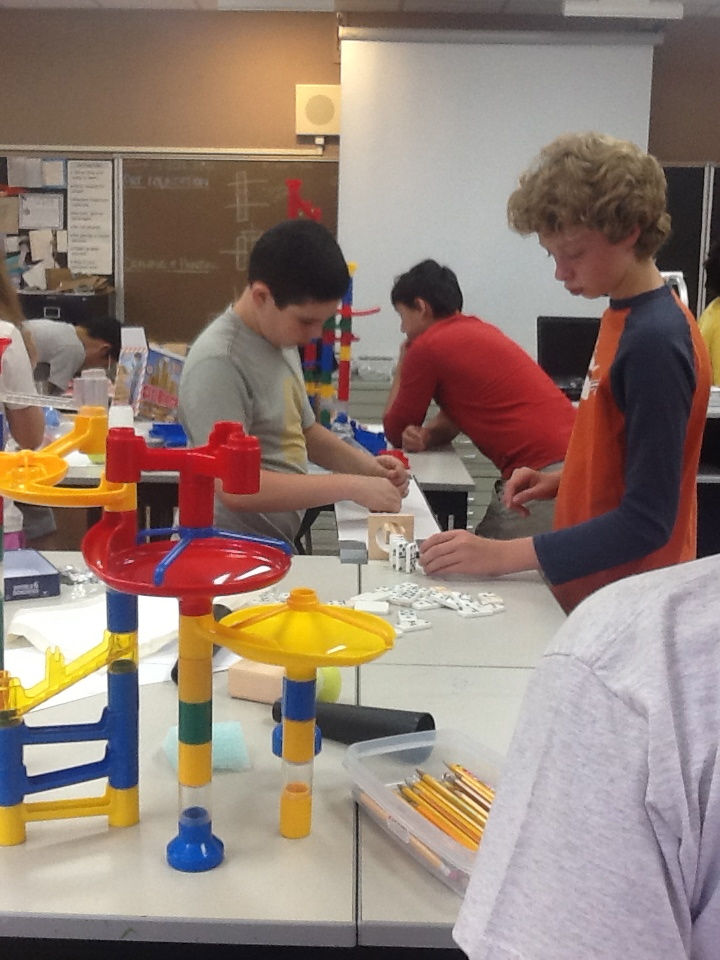
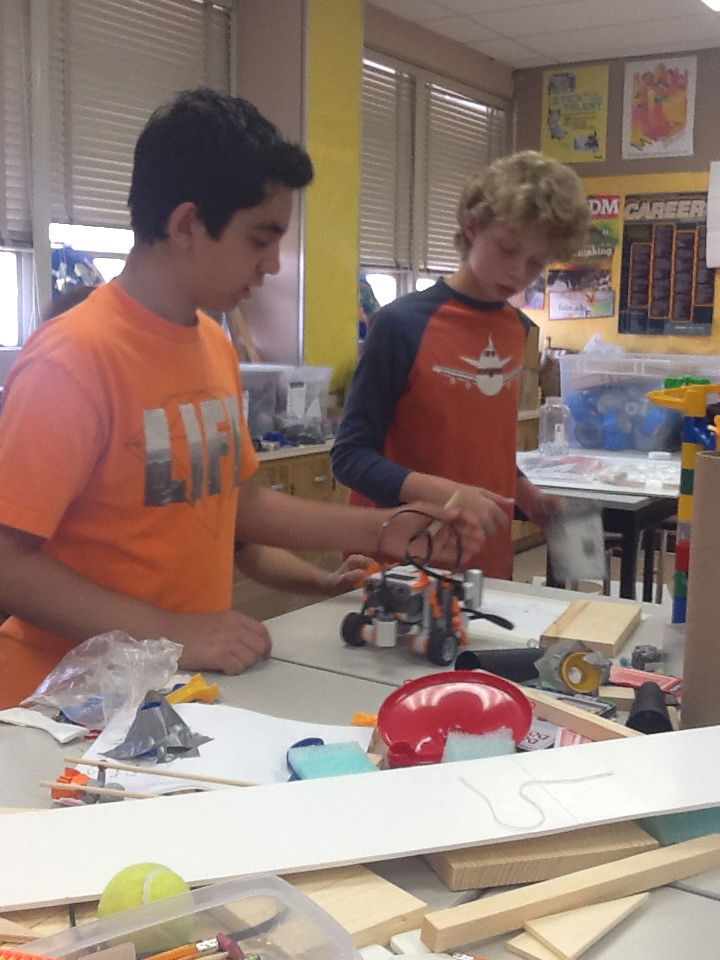
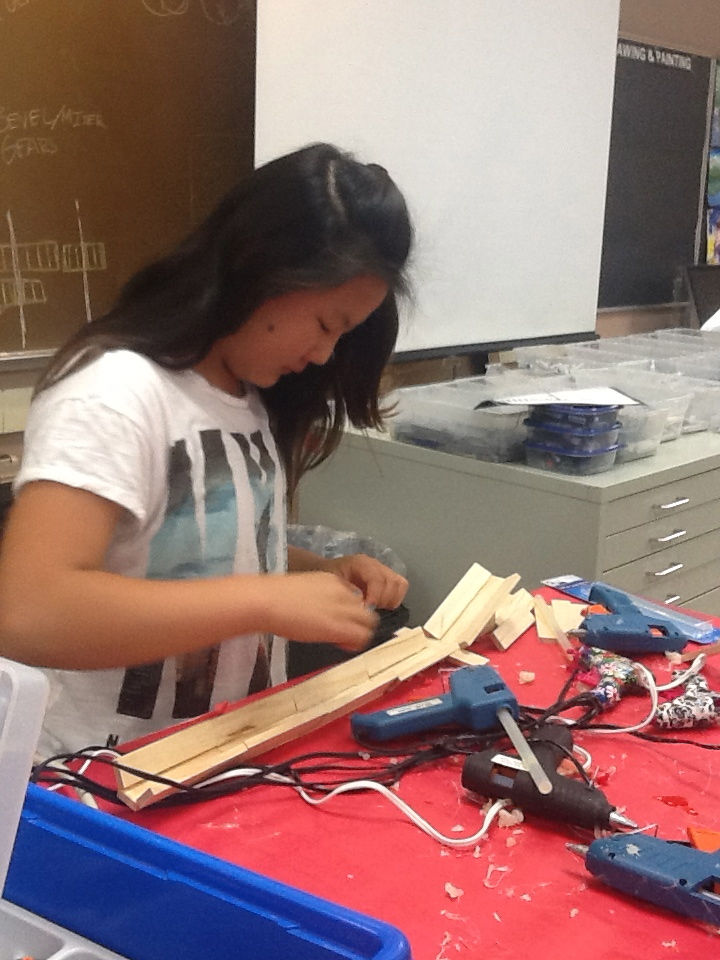

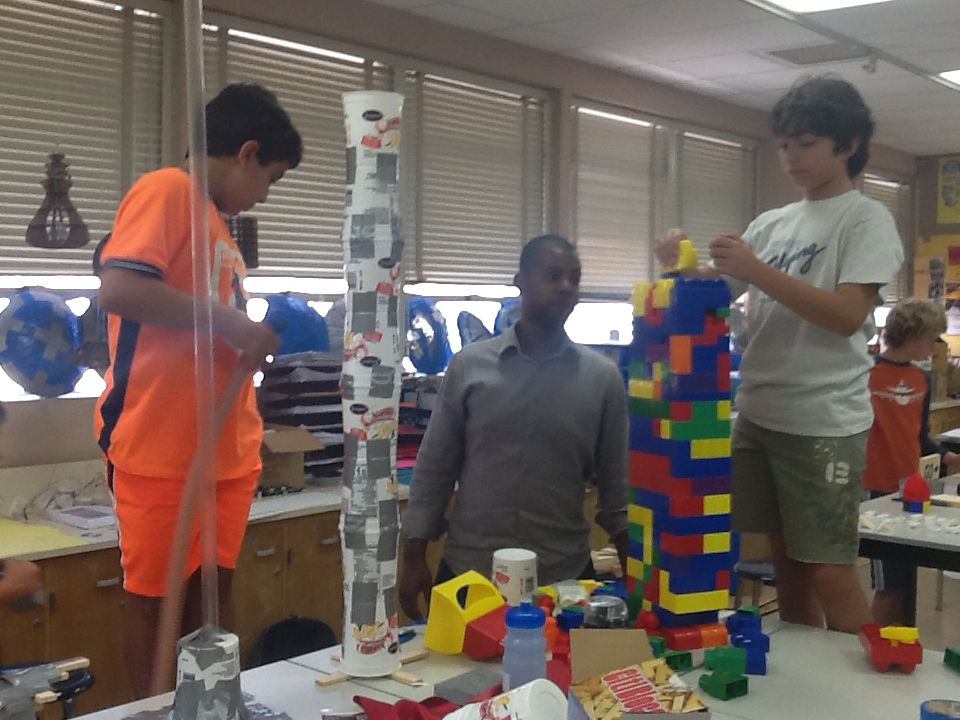


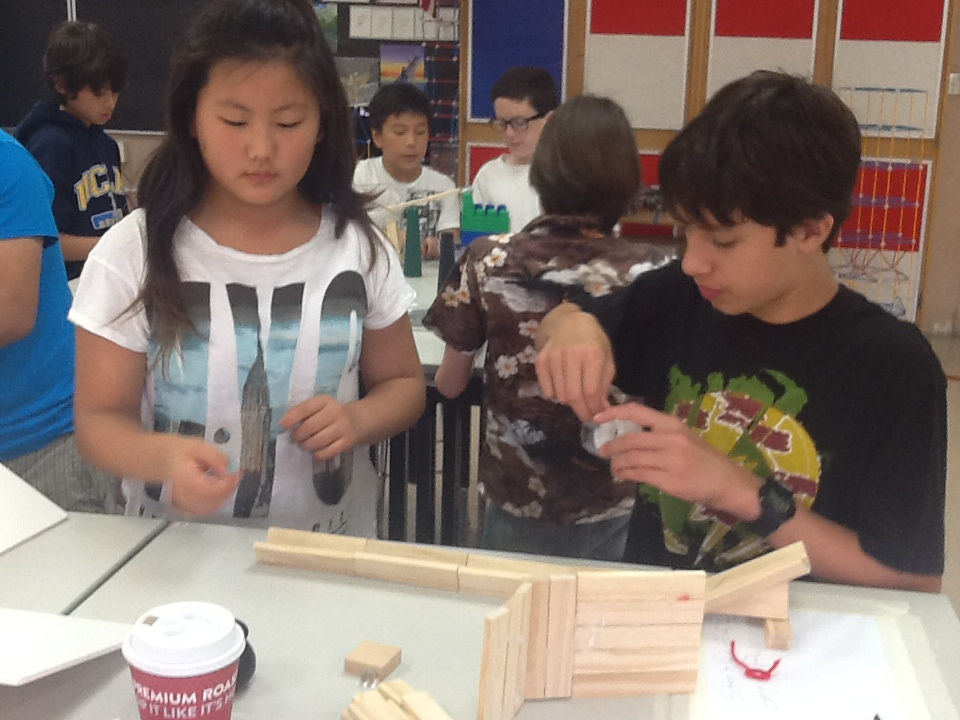


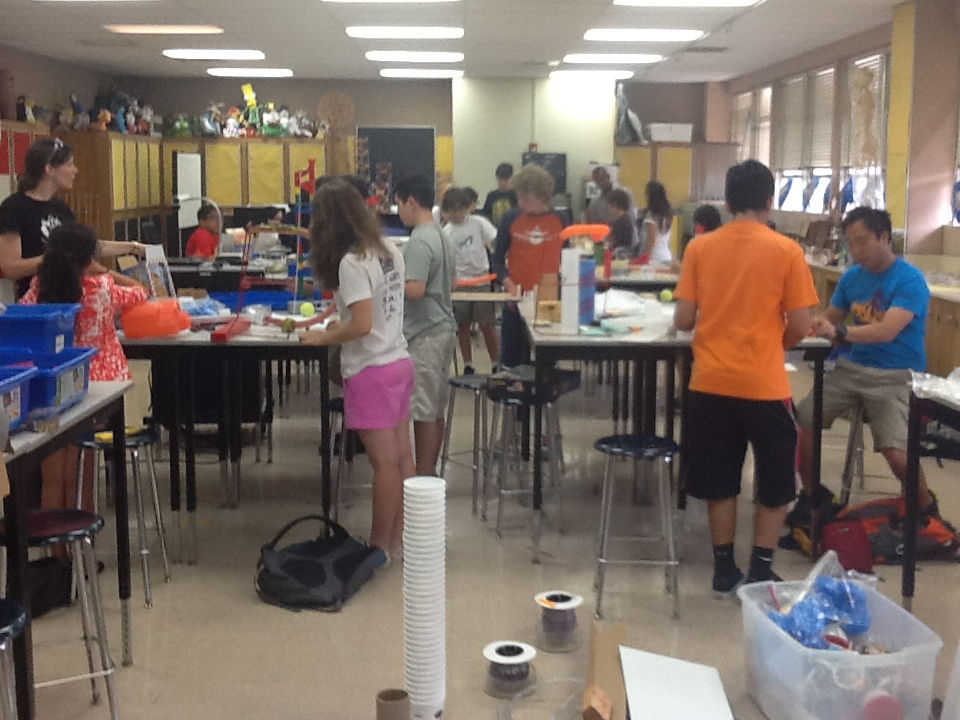

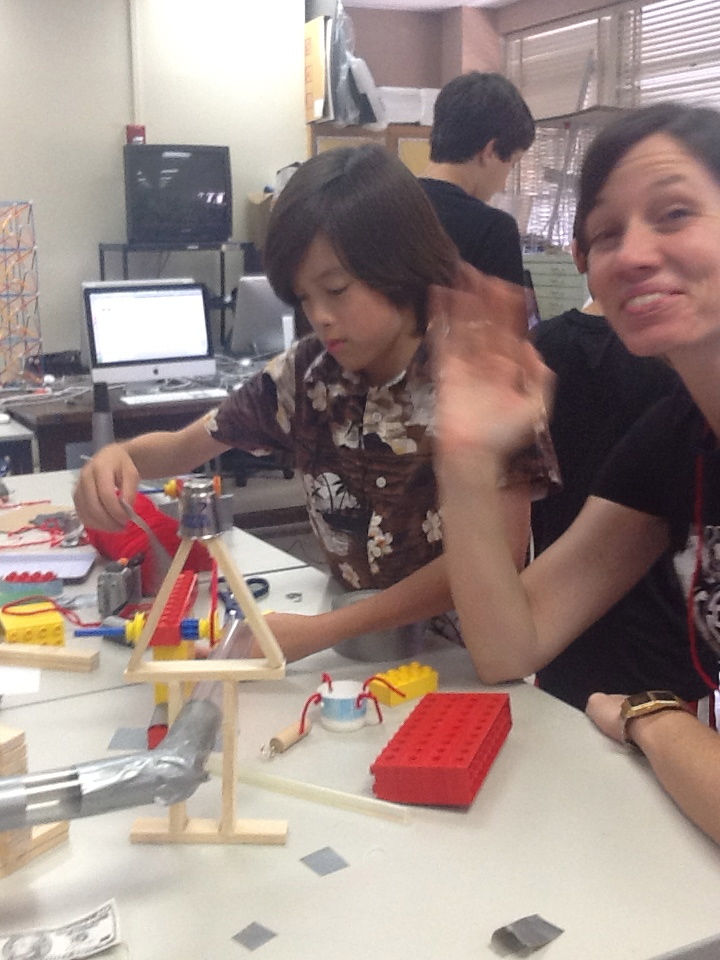

AND LASTLY...
SOME MORE PHOTOS!



